Title: Triumph in Technology: McDonald’s Ice Cream Machines Finally Fixed
Introduction:
For decades, the notorious unreliability of McDonald’s ice cream machines has been a source of frustration for customers and a running joke in popular culture. The frequent “out of order” signs have become an expected disappointment for those craving a McFlurry or a soft-serve cone. However, a groundbreaking technological advancement has finally addressed this long-standing issue, marking a significant triumph in the fast-food industry. Through innovative engineering and strategic partnerships, McDonald’s has successfully overhauled its ice cream machine operations, ensuring consistent availability and improved customer satisfaction. This development not only enhances the dining experience but also represents a pivotal moment in the intersection of technology and everyday convenience.
The Evolution Of McDonald’s Ice Cream Machines: A Technological Triumph
For decades, McDonald’s ice cream machines have been the subject of widespread frustration and countless internet memes, often criticized for their frequent malfunctions and unavailability. This long-standing issue has not only been a source of disappointment for customers craving a McFlurry or a soft-serve cone but has also posed operational challenges for the fast-food giant. However, recent technological advancements have ushered in a new era for McDonald’s, as the company has finally addressed and resolved the persistent problems plaguing its ice cream machines. This triumph in technology marks a significant milestone in the evolution of McDonald’s service delivery, promising a more reliable and satisfying experience for customers worldwide.
The journey to fixing McDonald’s ice cream machines has been a complex one, involving a combination of innovative engineering, strategic partnerships, and a commitment to enhancing customer satisfaction. Initially, the machines’ frequent breakdowns were attributed to their intricate design and the rigorous cleaning protocols required to maintain hygiene standards. These factors often led to extended downtime, as staff struggled to keep the machines operational. Recognizing the need for a comprehensive solution, McDonald’s embarked on a mission to overhaul its ice cream machine technology.
Central to this technological triumph was McDonald’s collaboration with tech companies specializing in food service equipment. By leveraging the expertise of these partners, McDonald’s was able to redesign its ice cream machines, focusing on simplifying their mechanics and improving their reliability. The new machines feature advanced diagnostic systems that can detect potential issues before they lead to breakdowns, allowing for proactive maintenance and reducing the likelihood of unexpected failures. This innovation not only minimizes downtime but also ensures that customers can consistently enjoy their favorite frozen treats.
Moreover, the integration of smart technology into the ice cream machines has revolutionized their operation. Equipped with IoT (Internet of Things) capabilities, the machines can now communicate with McDonald’s central systems, providing real-time data on their performance and maintenance needs. This connectivity enables McDonald’s to monitor the machines remotely, ensuring that any issues are promptly addressed and resolved. As a result, the company can maintain a higher standard of service, enhancing the overall customer experience.
In addition to technological improvements, McDonald’s has also invested in comprehensive training programs for its staff, ensuring that they are well-equipped to operate and maintain the new machines. By empowering employees with the knowledge and skills needed to manage the equipment effectively, McDonald’s has further reduced the risk of machine malfunctions and improved the efficiency of its service delivery.
The successful resolution of the ice cream machine issue is a testament to McDonald’s commitment to innovation and customer satisfaction. By embracing cutting-edge technology and fostering strategic partnerships, the company has not only addressed a long-standing problem but has also set a new standard for operational excellence in the fast-food industry. This achievement underscores the importance of continuous improvement and adaptation in a rapidly evolving technological landscape.
As McDonald’s ice cream machines continue to operate smoothly, customers can look forward to a more reliable and enjoyable experience, free from the frustration of unavailable treats. This technological triumph not only enhances McDonald’s reputation but also reinforces its position as a leader in the fast-food sector, demonstrating the power of innovation in overcoming challenges and driving success.
Behind The Scenes: How Technology Resolved The McDonald’s Ice Cream Machine Dilemma
For years, the notorious unreliability of McDonald’s ice cream machines has been a source of frustration for customers and a running joke on social media. The frequent breakdowns of these machines have led to countless disappointments for those craving a McFlurry or a soft-serve cone. However, recent advancements in technology have finally addressed this long-standing issue, bringing a sense of triumph to both McDonald’s and its patrons. The resolution of this dilemma is a testament to the power of innovation and collaboration in overcoming persistent challenges.
The journey to fixing McDonald’s ice cream machines began with a thorough analysis of the underlying problems. These machines, known for their complexity, often required extensive cleaning cycles and were prone to malfunctions. The intricate design, while intended to ensure product quality, inadvertently led to frequent breakdowns. Recognizing the need for a comprehensive solution, McDonald’s partnered with tech companies to explore ways to enhance the reliability and efficiency of their ice cream machines.
One of the pivotal breakthroughs came with the introduction of advanced diagnostic software. This software, developed by a team of engineers, was designed to monitor the machines in real-time, identifying potential issues before they led to complete breakdowns. By providing detailed insights into the machine’s operations, the software enabled McDonald’s staff to perform timely maintenance and address minor problems before they escalated. This proactive approach significantly reduced downtime and improved the overall performance of the machines.
In addition to diagnostic software, the collaboration also led to the development of user-friendly interfaces for the machines. These interfaces simplified the operation and maintenance processes, making it easier for staff to manage the machines effectively. By streamlining these procedures, McDonald’s was able to minimize human error, which had previously contributed to machine failures. The combination of advanced technology and intuitive design proved to be a game-changer in resolving the ice cream machine dilemma.
Moreover, the implementation of remote monitoring capabilities further enhanced the reliability of the machines. This feature allowed technicians to access machine data remotely, enabling them to provide support and guidance without the need for on-site visits. As a result, issues could be addressed more swiftly, reducing the time machines were out of service. The integration of remote monitoring not only improved machine uptime but also optimized the overall maintenance process.
The successful resolution of the ice cream machine issue at McDonald’s underscores the importance of embracing technological advancements to solve complex problems. By leveraging cutting-edge solutions and fostering collaboration with tech experts, McDonald’s was able to transform a long-standing challenge into a triumph. This achievement not only enhances customer satisfaction but also sets a precedent for other industries facing similar operational hurdles.
In conclusion, the fixing of McDonald’s ice cream machines is a remarkable example of how technology can be harnessed to address persistent issues. Through the implementation of diagnostic software, user-friendly interfaces, and remote monitoring capabilities, McDonald’s has significantly improved the reliability of its ice cream machines. This triumph in technology not only delights customers but also demonstrates the potential for innovation to drive positive change in the fast-food industry. As McDonald’s continues to embrace technological advancements, it paves the way for a future where operational challenges are met with effective and sustainable solutions.
Customer Satisfaction Soars: The Impact Of Fixed Ice Cream Machines At McDonald’s
In recent years, McDonald’s ice cream machines have become infamous for their frequent malfunctions, often leaving customers disappointed and craving their favorite frozen treats. This persistent issue has not only been a source of frustration for patrons but also a challenge for the fast-food giant, as it struggled to maintain customer satisfaction and uphold its reputation for reliable service. However, a significant breakthrough has been achieved, as McDonald’s has finally addressed the problem, leading to a remarkable improvement in customer satisfaction.
The resolution of the ice cream machine dilemma can be attributed to a combination of technological advancements and strategic partnerships. McDonald’s collaborated with a team of engineers and technology experts to develop a more robust and efficient machine that minimizes the likelihood of breakdowns. This new generation of ice cream machines incorporates cutting-edge technology, including advanced sensors and self-diagnostic capabilities, which allow for real-time monitoring and maintenance alerts. Consequently, these machines are less prone to the mechanical failures that plagued their predecessors.
Moreover, McDonald’s has partnered with a specialized service provider to ensure timely and effective maintenance of the machines. This partnership has established a streamlined process for addressing any technical issues that may arise, thereby reducing downtime and ensuring that customers can consistently enjoy their favorite ice cream products. The combination of improved machinery and enhanced maintenance protocols has resulted in a significant reduction in the frequency of machine malfunctions, much to the delight of McDonald’s patrons.
The impact of these improvements on customer satisfaction cannot be overstated. With the ice cream machines now functioning reliably, customers are able to indulge in popular menu items such as the McFlurry, soft-serve cones, and sundaes without the disappointment of being told that the machine is out of order. This consistency in product availability has led to a noticeable increase in customer satisfaction scores, as patrons appreciate the enhanced reliability and service quality.
Furthermore, the resolution of the ice cream machine issue has had a positive effect on McDonald’s brand image. The company has demonstrated its commitment to addressing customer concerns and investing in technological solutions to enhance the overall dining experience. This proactive approach has not only restored customer confidence but also attracted new patrons who may have previously been deterred by the negative reputation surrounding the ice cream machines.
In addition to boosting customer satisfaction, the fixed ice cream machines have also contributed to increased sales and revenue for McDonald’s. With the machines now operational, the company has been able to capitalize on the high demand for its frozen desserts, particularly during peak seasons and promotional periods. This has resulted in a notable uptick in sales figures, further solidifying McDonald’s position as a leader in the fast-food industry.
In conclusion, the successful resolution of the ice cream machine issue at McDonald’s represents a triumph in technology and customer service. Through strategic partnerships and innovative solutions, the company has effectively addressed a longstanding problem, leading to a significant improvement in customer satisfaction and brand perception. As McDonald’s continues to prioritize technological advancements and customer-centric initiatives, it sets a precedent for the industry, demonstrating the importance of adapting to consumer needs and leveraging technology to enhance the overall dining experience.
The Role Of Innovation In Solving McDonald’s Ice Cream Machine Issues
For years, the notorious unreliability of McDonald’s ice cream machines has been a source of frustration for customers and a running joke on social media. The frequent breakdowns of these machines have led to countless disappointments for those craving a McFlurry or a soft-serve cone. However, recent advancements in technology have finally addressed this long-standing issue, marking a significant triumph in the realm of fast-food service. This development underscores the critical role of innovation in solving persistent operational challenges.
The problem with McDonald’s ice cream machines was not merely a matter of mechanical failure but also one of complexity. The machines required extensive cleaning cycles, which often led to downtime. Moreover, their intricate design made them prone to malfunctions that were difficult to diagnose and repair. This situation was exacerbated by the fact that only specialized technicians could service these machines, leading to delays in getting them back up and running. Consequently, the need for a more reliable and user-friendly solution became increasingly apparent.
Enter the world of technological innovation, where creative minds have been hard at work devising solutions to this vexing problem. A breakthrough came with the development of a new diagnostic tool that allows for real-time monitoring and troubleshooting of the ice cream machines. This tool, designed by a tech-savvy startup, provides McDonald’s staff with immediate insights into the machine’s status, enabling them to address issues before they lead to complete breakdowns. By integrating this technology, McDonald’s has significantly reduced the downtime of its ice cream machines, much to the delight of its customers.
Furthermore, the implementation of predictive maintenance has played a pivotal role in this success story. By utilizing data analytics and machine learning algorithms, McDonald’s can now anticipate potential failures before they occur. This proactive approach not only minimizes disruptions but also extends the lifespan of the machines. The ability to predict and prevent malfunctions represents a paradigm shift in how McDonald’s manages its equipment, showcasing the transformative power of innovation.
In addition to these technological advancements, McDonald’s has also invested in training its staff to better understand and operate the new systems. This comprehensive approach ensures that employees are equipped with the necessary skills to maintain the machines effectively, further reducing the likelihood of issues arising. By empowering its workforce with knowledge and tools, McDonald’s has created a more resilient operational framework.
The resolution of the ice cream machine dilemma is a testament to the importance of embracing innovation in addressing operational challenges. It highlights how technology can be leveraged to enhance customer satisfaction and streamline business processes. As McDonald’s continues to refine its approach, other fast-food chains may look to this success as a model for overcoming their own equipment-related hurdles.
In conclusion, the triumph over the notorious ice cream machine issues at McDonald’s serves as a compelling example of how innovation can drive meaningful change. By harnessing the power of technology, McDonald’s has not only solved a long-standing problem but also set a new standard for operational excellence in the fast-food industry. This achievement underscores the potential for innovation to transform challenges into opportunities, paving the way for a more efficient and customer-centric future.
A Sweet Success: The Technology That Transformed McDonald’s Dessert Experience
For decades, McDonald’s ice cream machines have been the subject of widespread frustration and countless internet memes, as customers frequently encountered the dreaded “out of order” sign when craving a sweet treat. This persistent issue, which seemed to defy resolution, has finally met its match through a groundbreaking technological advancement. The triumph in technology that has transformed McDonald’s dessert experience is not only a testament to innovation but also a significant step forward in customer satisfaction.
The journey to fixing McDonald’s ice cream machines began with a thorough analysis of the underlying problems. Historically, these machines were notorious for their complex cleaning cycles and frequent malfunctions, which often required specialized technicians to address. This led to prolonged downtimes and a negative impact on customer experience. Recognizing the need for a comprehensive solution, McDonald’s partnered with a team of engineers and technology experts to develop a more reliable and efficient system.
The result of this collaboration is a state-of-the-art diagnostic and maintenance technology that has been integrated into the ice cream machines. This new system employs advanced sensors and real-time monitoring capabilities to detect potential issues before they lead to machine failure. By providing early warnings and detailed diagnostics, the technology enables restaurant staff to address minor problems promptly, thereby reducing the likelihood of extended outages. Moreover, the system’s user-friendly interface simplifies the maintenance process, allowing employees to perform routine checks and cleaning with ease.
In addition to improving machine reliability, the new technology has also enhanced the overall quality of McDonald’s ice cream products. The precise temperature control and automated mixing processes ensure a consistently smooth and creamy texture, elevating the dessert experience for customers. This consistency not only meets but often exceeds customer expectations, reinforcing McDonald’s commitment to delivering high-quality products.
Furthermore, the implementation of this technology aligns with McDonald’s broader sustainability goals. By reducing the frequency of machine breakdowns and the need for external repairs, the company has minimized its carbon footprint associated with service calls and replacement parts. This eco-friendly approach reflects McDonald’s dedication to integrating sustainable practices into its operations, thereby contributing to a more environmentally conscious business model.
The successful resolution of the ice cream machine dilemma has also had a positive impact on McDonald’s brand image. By addressing a long-standing issue that had become a cultural touchpoint, the company has demonstrated its responsiveness to customer feedback and its willingness to invest in technological solutions. This proactive approach has not only restored customer confidence but also strengthened McDonald’s position as a leader in the fast-food industry.
In conclusion, the triumph in technology that has finally fixed McDonald’s ice cream machines represents a significant milestone in the company’s ongoing efforts to enhance customer satisfaction and operational efficiency. Through innovative engineering and strategic partnerships, McDonald’s has transformed a persistent challenge into an opportunity for growth and improvement. As a result, customers can now enjoy their favorite frozen treats with greater reliability and quality, marking a sweet success in the ever-evolving landscape of fast-food technology.
Lessons Learned: How McDonald’s Overcame Its Ice Cream Machine Challenges Through Technology
For years, McDonald’s ice cream machines have been the subject of widespread frustration and countless internet memes, as customers frequently encountered the dreaded “out of order” sign when craving a McFlurry or a soft-serve cone. This persistent issue, which seemed to defy resolution, became emblematic of a larger challenge within the fast-food industry: maintaining consistent and reliable service in the face of technological shortcomings. However, recent developments have marked a turning point in this saga, as McDonald’s has successfully addressed these challenges through innovative technological solutions.
The journey to resolving the ice cream machine conundrum began with a comprehensive analysis of the underlying issues. McDonald’s identified that the machines’ frequent breakdowns were primarily due to their complex cleaning cycles and the intricate nature of their mechanical components. These factors often led to prolonged downtime, as staff struggled to navigate the machines’ cumbersome maintenance requirements. Recognizing the need for a more efficient solution, McDonald’s turned to technology to streamline operations and enhance machine reliability.
In collaboration with tech companies specializing in food service equipment, McDonald’s embarked on a mission to redesign its ice cream machines. The goal was to create a system that was not only easier to maintain but also more resilient to the demands of high-volume service. By integrating advanced diagnostic tools and real-time monitoring capabilities, the new machines could now alert staff to potential issues before they resulted in complete breakdowns. This proactive approach significantly reduced downtime and improved overall service efficiency.
Moreover, McDonald’s leveraged the power of data analytics to gain insights into machine performance and maintenance patterns. By analyzing data collected from various locations, the company was able to identify common failure points and implement targeted improvements. This data-driven strategy not only enhanced the machines’ reliability but also informed staff training programs, ensuring that employees were better equipped to handle routine maintenance tasks.
The implementation of these technological advancements was not without its challenges. McDonald’s had to invest in extensive training programs to familiarize staff with the new systems and ensure a smooth transition. Additionally, the company had to navigate the logistical complexities of rolling out the updated machines across its vast network of restaurants. However, the commitment to overcoming these hurdles underscored McDonald’s dedication to enhancing customer satisfaction and operational efficiency.
As a result of these efforts, McDonald’s has witnessed a significant reduction in ice cream machine-related complaints and an increase in customer satisfaction. The successful resolution of this long-standing issue serves as a testament to the power of technology in addressing operational challenges. It also highlights the importance of adaptability and innovation in maintaining a competitive edge in the fast-food industry.
In conclusion, McDonald’s triumph over its ice cream machine challenges offers valuable lessons for businesses facing similar technological hurdles. By embracing innovation, leveraging data analytics, and investing in employee training, companies can overcome even the most persistent operational issues. As McDonald’s continues to refine its technological solutions, it sets a precedent for the industry, demonstrating that with the right approach, even the most notorious problems can be transformed into opportunities for growth and improvement.
Q&A
1. **Question:** What is the main issue with McDonald’s ice cream machines?
**Answer:** The main issue with McDonald’s ice cream machines has been their frequent breakdowns and the complexity involved in repairing them.
2. **Question:** Who developed a solution to fix McDonald’s ice cream machines?
**Answer:** A startup called Kytch developed a solution to fix McDonald’s ice cream machines by creating a device that provides better diagnostics and control.
3. **Question:** How does the Kytch device work?
**Answer:** The Kytch device works by connecting to the ice cream machines and offering real-time data and insights, allowing operators to diagnose and fix issues more efficiently.
4. **Question:** What has been McDonald’s response to the Kytch device?
**Answer:** McDonald’s has been resistant to the Kytch device, citing concerns over safety and unauthorized modifications to their equipment.
5. **Question:** What impact has the Kytch device had on franchise owners?
**Answer:** Franchise owners who have used the Kytch device have reported improved uptime and reduced maintenance costs for their ice cream machines.
6. **Question:** What legal actions have arisen from the Kytch solution?
**Answer:** Legal actions have arisen between Kytch and McDonald’s, with Kytch suing McDonald’s for allegedly interfering with their business and spreading false information about their product.The conclusion of “Triumph in Technology: McDonald’s Ice Cream Machines Finally Fixed” highlights a significant breakthrough in addressing a long-standing issue that has frustrated both customers and franchise owners. The successful resolution of the persistent problems with McDonald’s ice cream machines represents a triumph of innovation and collaboration, likely involving improved technology, better maintenance protocols, or enhanced training for staff. This development not only enhances customer satisfaction by ensuring consistent availability of popular ice cream products but also streamlines operations and reduces downtime for franchisees. Ultimately, this achievement underscores the importance of technological advancements in solving practical challenges within the fast-food industry, setting a precedent for future improvements in service and efficiency.
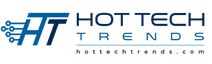