Breakthroughs in robotic dexterity have marked a significant leap forward in the field of robotics, transforming the way machines interact with their environment and perform complex tasks. Recent innovations have focused on enhancing the precision, adaptability, and sensory capabilities of robotic systems, enabling them to mimic human-like dexterity with unprecedented accuracy. These advancements are driven by cutting-edge developments in artificial intelligence, machine learning, and sensor technology, allowing robots to perform intricate manipulations, handle delicate objects, and adapt to dynamic environments. As a result, industries ranging from manufacturing and healthcare to logistics and service sectors are witnessing a revolution in automation, where robots are not only tools but collaborative partners capable of executing tasks with finesse and reliability. This new era of robotic dexterity promises to redefine productivity, efficiency, and innovation across various domains, paving the way for a future where human-robot collaboration reaches new heights.
Enhancing Precision: The Role of AI in Robotic Dexterity
In recent years, the field of robotics has witnessed remarkable advancements, particularly in the realm of robotic dexterity. This progress is largely attributed to the integration of artificial intelligence (AI), which has significantly enhanced the precision and adaptability of robotic systems. As we delve into the intricacies of these innovations, it becomes evident that AI plays a pivotal role in transforming robotic dexterity from a theoretical concept into a practical reality.
To begin with, the incorporation of AI into robotic systems has enabled machines to perform tasks with a level of precision that was previously unattainable. Traditional robotic systems relied heavily on pre-programmed instructions, which limited their ability to adapt to dynamic environments. However, with the advent of AI, robots can now learn from their surroundings and make real-time adjustments. This capability is particularly crucial in industries such as manufacturing and healthcare, where precision is paramount. For instance, in surgical applications, AI-powered robots can execute complex procedures with minimal human intervention, thereby reducing the risk of errors and improving patient outcomes.
Moreover, AI enhances robotic dexterity by enabling machines to process and interpret vast amounts of data. Through machine learning algorithms, robots can analyze sensory inputs, such as visual and tactile information, to make informed decisions. This ability to process data in real-time allows robots to perform intricate tasks that require a high degree of precision. For example, in the assembly of delicate electronic components, AI-driven robots can identify and rectify misalignments with remarkable accuracy, ensuring that each component is placed correctly.
In addition to improving precision, AI also facilitates the development of more versatile robotic systems. By leveraging deep learning techniques, robots can acquire new skills and adapt to a wide range of tasks. This adaptability is crucial in environments where conditions are constantly changing. For instance, in agricultural settings, AI-enabled robots can adjust their actions based on variations in crop growth and weather conditions, thereby optimizing yield and efficiency.
Furthermore, the integration of AI in robotic systems has led to the creation of collaborative robots, or cobots, which are designed to work alongside humans. These robots are equipped with advanced sensors and AI algorithms that enable them to understand and predict human actions. As a result, cobots can assist in tasks that require a high level of dexterity, such as assembling intricate machinery or handling fragile materials. This collaboration not only enhances productivity but also ensures a safer working environment by reducing the likelihood of accidents.
As we continue to explore the potential of AI in enhancing robotic dexterity, it is important to acknowledge the challenges that accompany these advancements. One of the primary concerns is the ethical implications of increased automation, particularly in terms of job displacement. However, by focusing on the development of collaborative systems that augment human capabilities, we can mitigate these concerns and harness the full potential of AI-driven robotics.
In conclusion, the role of AI in enhancing robotic dexterity is undeniable. Through improved precision, adaptability, and collaboration, AI is revolutionizing the way robots interact with their environments and perform complex tasks. As we move forward, continued research and innovation in this field will undoubtedly lead to even more groundbreaking developments, further solidifying the integral role of AI in the future of robotics.
Soft Robotics: Mimicking Human Touch for Delicate Tasks
In recent years, the field of robotics has witnessed remarkable advancements, particularly in the realm of soft robotics, which aims to mimic the nuanced dexterity of human touch. This burgeoning area of research focuses on creating robots capable of performing delicate tasks with precision and care, a feat that has long eluded traditional rigid robotic systems. The latest innovations in soft robotics are poised to revolutionize industries ranging from healthcare to manufacturing, offering unprecedented levels of adaptability and sensitivity.
One of the primary challenges in developing soft robotic systems is replicating the intricate mechanics of the human hand. Human touch is not only about strength but also about the ability to apply varying degrees of pressure and adapt to the shape and texture of objects. To address this, researchers have turned to materials science, developing flexible, compliant materials that can bend and stretch in ways that rigid components cannot. These materials, often inspired by biological tissues, allow robots to interact with their environment in a more human-like manner, providing the necessary dexterity for handling fragile items.
Moreover, the integration of advanced sensors has been pivotal in enhancing the tactile capabilities of soft robots. These sensors, embedded within the soft materials, can detect minute changes in pressure, temperature, and texture, enabling the robot to adjust its grip accordingly. This sensory feedback loop is akin to the human nervous system, where information is continuously processed to refine movements. Consequently, soft robots can perform tasks that require a gentle touch, such as picking ripe fruit without causing damage or assisting in surgical procedures where precision is paramount.
In addition to material and sensor innovations, the development of sophisticated control algorithms has been instrumental in advancing soft robotic dexterity. These algorithms, often powered by artificial intelligence, allow robots to learn from their interactions and improve their performance over time. By analyzing data from previous tasks, the robots can predict the best approach for handling new challenges, thereby increasing their efficiency and effectiveness. This learning capability is crucial for applications in dynamic environments where conditions can change rapidly.
The implications of these breakthroughs are far-reaching. In the medical field, for instance, soft robots are being developed to assist surgeons in performing minimally invasive procedures, reducing recovery times and improving patient outcomes. In agriculture, they offer a solution to the labor-intensive task of harvesting delicate crops, ensuring that produce reaches consumers in optimal condition. Furthermore, in manufacturing, soft robots can handle delicate components with care, reducing waste and improving product quality.
Despite these advancements, challenges remain in the widespread adoption of soft robotics. The complexity of designing systems that can seamlessly integrate into existing workflows and the cost of developing and maintaining these advanced technologies are significant hurdles. However, ongoing research and collaboration between academia and industry are paving the way for more accessible and affordable solutions.
In conclusion, the latest innovations in soft robotics are transforming the landscape of robotic dexterity, bringing us closer to machines that can mimic the human touch with remarkable accuracy. As these technologies continue to evolve, they hold the promise of enhancing our ability to perform delicate tasks across various sectors, ultimately improving efficiency and quality of life. The journey towards perfecting robotic dexterity is ongoing, but the strides made thus far are a testament to the potential of soft robotics in shaping the future.
Advanced Sensors: Revolutionizing Robotic Hand-Eye Coordination
In recent years, the field of robotics has witnessed remarkable advancements, particularly in the realm of robotic dexterity. Central to these developments is the integration of advanced sensors, which have revolutionized robotic hand-eye coordination. This innovation has not only enhanced the precision and efficiency of robotic systems but also expanded their applicability across various industries. As we delve into the intricacies of these advancements, it becomes evident that the synergy between sensors and robotics is paving the way for a new era of automation.
To begin with, the role of sensors in robotic systems cannot be overstated. These devices serve as the eyes and ears of robots, enabling them to perceive and interpret their environment with unprecedented accuracy. In the context of robotic dexterity, sensors facilitate the intricate coordination between a robot’s visual and motor systems. This coordination is crucial for tasks that require fine manipulation and precise control, such as assembling delicate components or performing intricate surgical procedures. By providing real-time feedback, sensors allow robots to adjust their actions dynamically, thereby enhancing their adaptability and performance.
Moreover, the integration of advanced sensors has led to significant improvements in the spatial awareness of robotic systems. Through the use of high-resolution cameras and depth sensors, robots can now construct detailed three-dimensional maps of their surroundings. This capability is instrumental in enabling robots to navigate complex environments and interact with objects in a more human-like manner. For instance, in manufacturing settings, robots equipped with these sensors can identify and manipulate parts with varying shapes and sizes, thereby streamlining production processes and reducing the likelihood of errors.
In addition to visual sensors, tactile sensors have also played a pivotal role in advancing robotic dexterity. These sensors mimic the sense of touch, allowing robots to gauge the texture, temperature, and pressure of objects they handle. This sensory feedback is crucial for tasks that require delicate handling, such as sorting fragile items or performing precision assembly. By emulating the human sense of touch, tactile sensors enable robots to perform tasks with a level of finesse that was previously unattainable.
Furthermore, the integration of machine learning algorithms with sensor data has further enhanced the capabilities of robotic systems. By analyzing vast amounts of sensory data, these algorithms enable robots to learn from their experiences and improve their performance over time. This learning process is akin to the way humans refine their motor skills through practice and repetition. Consequently, robots can now adapt to new tasks and environments with remarkable speed and efficiency, making them invaluable assets in dynamic and unpredictable settings.
As we look to the future, the potential applications of advanced sensors in robotics are virtually limitless. From healthcare and manufacturing to agriculture and logistics, the ability of robots to perform complex tasks with precision and dexterity is set to transform industries across the board. However, it is important to acknowledge the challenges that accompany these advancements. Ensuring the reliability and safety of robotic systems remains a paramount concern, particularly in applications where human lives are at stake.
In conclusion, the integration of advanced sensors has undeniably revolutionized robotic hand-eye coordination, ushering in a new era of robotic dexterity. By enhancing the sensory capabilities of robots, these innovations have expanded their potential applications and improved their performance across various domains. As research and development in this field continue to progress, we can anticipate even more groundbreaking advancements that will further redefine the landscape of robotics.
Machine Learning: Teaching Robots to Adapt and Improve
In recent years, the field of robotics has witnessed remarkable advancements, particularly in the realm of robotic dexterity. These breakthroughs have been largely driven by innovations in machine learning, which have enabled robots to adapt and improve their capabilities in unprecedented ways. As we delve into the intricacies of these developments, it becomes evident that machine learning is not merely a tool but a transformative force that is reshaping the landscape of robotic dexterity.
To begin with, machine learning algorithms have empowered robots to learn from their environments and experiences, much like humans do. This ability to learn and adapt is crucial for enhancing robotic dexterity, as it allows robots to perform complex tasks with greater precision and efficiency. For instance, through reinforcement learning, robots can be trained to optimize their movements by receiving feedback from their actions. This iterative process enables them to refine their skills over time, leading to improved performance in tasks such as object manipulation and assembly.
Moreover, the integration of deep learning techniques has further augmented the capabilities of robots. By leveraging neural networks, robots can process vast amounts of data and recognize patterns that were previously beyond their reach. This has significant implications for robotic dexterity, as it allows robots to understand and interpret the nuances of their surroundings. Consequently, they can make informed decisions and execute tasks with a level of sophistication that was once thought to be exclusive to human operators.
In addition to these advancements, the development of simulation environments has played a pivotal role in enhancing robotic dexterity. These virtual platforms provide a safe and controlled space for robots to practice and hone their skills without the risk of real-world consequences. By simulating various scenarios and challenges, robots can experiment with different strategies and learn from their mistakes. This not only accelerates the learning process but also equips robots with the adaptability needed to tackle unforeseen obstacles in real-world applications.
Furthermore, the advent of collaborative learning has opened new avenues for improving robotic dexterity. By enabling robots to share knowledge and experiences with one another, collaborative learning fosters a collective intelligence that surpasses individual capabilities. This approach is particularly beneficial in environments where multiple robots are required to work in tandem, as it ensures seamless coordination and enhances overall efficiency. As a result, robots can perform intricate tasks that demand a high degree of dexterity, such as surgical procedures or intricate manufacturing processes.
Despite these remarkable achievements, challenges remain in the quest to perfect robotic dexterity. One of the primary hurdles is the development of tactile sensors that can replicate the sensitivity and precision of human touch. While significant progress has been made in this area, further research is needed to create sensors that can provide robots with the nuanced feedback required for delicate tasks. Additionally, ethical considerations must be addressed to ensure that the deployment of highly dexterous robots aligns with societal values and norms.
In conclusion, the breakthroughs in robotic dexterity, driven by machine learning innovations, have ushered in a new era of possibilities. By enabling robots to learn, adapt, and improve, these advancements have paved the way for a future where robots can perform tasks with a level of dexterity that rivals human capabilities. As research continues to push the boundaries of what is possible, it is clear that the synergy between machine learning and robotics will continue to be a catalyst for transformative change in the years to come.
Collaborative Robots: Enhancing Dexterity in Human-Robot Teams
In recent years, the field of robotics has witnessed remarkable advancements, particularly in the realm of collaborative robots, often referred to as cobots. These innovations have significantly enhanced the dexterity of robots, enabling them to work alongside humans more effectively and safely. As industries increasingly integrate automation into their operations, the ability of robots to perform complex tasks with precision and adaptability has become paramount. This evolution in robotic dexterity is not only transforming manufacturing processes but also redefining the dynamics of human-robot teams.
One of the key breakthroughs in robotic dexterity is the development of advanced sensor technologies. These sensors allow robots to perceive their environment with heightened accuracy, facilitating more nuanced interactions with both objects and humans. For instance, tactile sensors embedded in robotic grippers can mimic the sensitivity of human touch, enabling robots to handle delicate items without causing damage. This capability is particularly beneficial in industries such as electronics and pharmaceuticals, where precision handling is crucial. Moreover, these sensors enhance safety by allowing robots to detect and respond to human presence, thereby reducing the risk of accidents in shared workspaces.
In addition to sensor advancements, the integration of artificial intelligence (AI) has played a pivotal role in enhancing robotic dexterity. Machine learning algorithms enable robots to learn from experience, improving their performance over time. This adaptability is essential in dynamic environments where tasks may vary or require customization. For example, in assembly lines, AI-powered robots can adjust their actions based on the specific requirements of each product, ensuring consistency and quality. Furthermore, AI facilitates better communication between robots and human workers, fostering a more collaborative and efficient workflow.
Another significant innovation is the development of flexible robotic arms that mimic the range of motion found in human limbs. These arms are equipped with multiple joints and actuators, allowing for intricate movements and rotations. This flexibility is crucial for tasks that require a high degree of precision, such as surgical procedures or intricate assembly work. By replicating the dexterity of human hands, these robotic arms can perform tasks that were previously deemed too complex for automation. Consequently, industries are witnessing a shift towards more sophisticated applications of robotics, where human-robot teams can tackle challenges that neither could address alone.
Moreover, the advent of cloud robotics has further enhanced the capabilities of collaborative robots. By leveraging cloud computing, robots can access vast amounts of data and computational power, enabling them to process information and make decisions in real-time. This connectivity allows for seamless collaboration between multiple robots and human operators, as they can share insights and coordinate actions more effectively. As a result, industries are experiencing increased productivity and efficiency, as robots can quickly adapt to changing conditions and optimize their performance.
In conclusion, the latest innovations in robotic dexterity are revolutionizing the way humans and robots collaborate. Through advancements in sensor technology, artificial intelligence, flexible robotic arms, and cloud robotics, cobots are becoming more adept at performing complex tasks with precision and adaptability. These developments are not only enhancing productivity across various industries but also fostering safer and more efficient human-robot interactions. As technology continues to evolve, the potential for collaborative robots to transform the workplace and drive innovation is boundless, paving the way for a future where humans and robots work together in harmony.
Real-World Applications: Robotic Dexterity in Healthcare and Manufacturing
In recent years, the field of robotics has witnessed remarkable advancements, particularly in the realm of robotic dexterity. These innovations have paved the way for significant improvements in both healthcare and manufacturing, two sectors that stand to benefit immensely from enhanced robotic capabilities. As we delve into the real-world applications of robotic dexterity, it becomes evident that these technological breakthroughs are not only transforming industries but also redefining the boundaries of what robots can achieve.
In the healthcare sector, robotic dexterity has emerged as a game-changer, offering unprecedented precision and control in surgical procedures. Surgeons are now able to perform minimally invasive surgeries with the assistance of robotic systems that mimic the intricate movements of the human hand. This level of precision reduces the risk of human error, minimizes patient recovery time, and enhances overall surgical outcomes. For instance, robotic-assisted surgeries in orthopedics and cardiology have shown promising results, with robots executing complex tasks such as suturing and tissue manipulation with remarkable accuracy. Moreover, the integration of artificial intelligence with robotic systems allows for real-time data analysis, enabling surgeons to make informed decisions during operations.
Transitioning to the manufacturing sector, robotic dexterity is revolutionizing production lines by enhancing efficiency and productivity. Robots equipped with advanced dexterous capabilities are now able to perform tasks that were once considered too intricate for automation. These tasks include assembling delicate components, handling fragile materials, and performing quality control inspections with a level of precision that surpasses human capabilities. As a result, manufacturers are experiencing reduced production costs, increased output, and improved product quality. Furthermore, the adaptability of these robots allows them to be reprogrammed for different tasks, providing manufacturers with the flexibility to respond swiftly to changing market demands.
The convergence of robotic dexterity with machine learning and sensor technologies has further expanded the potential applications of these systems. In healthcare, for example, robots are being developed to assist in rehabilitation therapies, where they can mimic human movements and provide personalized treatment plans for patients recovering from injuries or surgeries. This not only enhances the effectiveness of rehabilitation but also alleviates the burden on healthcare professionals. Similarly, in manufacturing, robots are being equipped with sensors that enable them to perceive and adapt to their environment, allowing for seamless collaboration with human workers on the factory floor. This human-robot collaboration is fostering a new era of smart manufacturing, where robots and humans work in tandem to achieve optimal results.
Despite these advancements, challenges remain in the widespread adoption of robotic dexterity. Issues such as high costs, technical complexities, and the need for specialized training pose significant barriers. However, ongoing research and development efforts are focused on addressing these challenges, with the aim of making robotic systems more accessible and user-friendly. As these obstacles are gradually overcome, the potential for robotic dexterity to transform healthcare and manufacturing becomes increasingly tangible.
In conclusion, the breakthroughs in robotic dexterity are ushering in a new era of innovation across various industries. By enhancing precision, efficiency, and adaptability, these advancements are not only improving existing processes but also opening up new possibilities for the future. As we continue to explore the real-world applications of robotic dexterity, it is clear that the impact of these innovations will be profound, shaping the way we approach complex tasks in healthcare and manufacturing for years to come.
Q&A
1. **What is robotic dexterity?**
Robotic dexterity refers to the ability of robots to manipulate objects with precision and skill, similar to human hand movements.
2. **What are some recent innovations in robotic dexterity?**
Recent innovations include advanced grippers with tactile sensors, AI-driven manipulation algorithms, and soft robotics that mimic human hand flexibility.
3. **How do tactile sensors improve robotic dexterity?**
Tactile sensors provide robots with feedback on pressure, texture, and slippage, allowing for more precise and adaptive manipulation of objects.
4. **What role does AI play in enhancing robotic dexterity?**
AI enables robots to learn from experience, improve their manipulation skills over time, and adapt to new tasks and environments.
5. **What is soft robotics, and how does it contribute to dexterity?**
Soft robotics involves using flexible materials to create robots that can handle delicate objects and perform complex tasks with greater ease and safety.
6. **What industries benefit from advancements in robotic dexterity?**
Industries such as manufacturing, healthcare, logistics, and agriculture benefit from improved robotic dexterity through increased efficiency and reduced human labor.Recent breakthroughs in robotic dexterity have significantly advanced the field, enabling robots to perform complex tasks with greater precision and adaptability. Innovations such as improved sensor technologies, advanced machine learning algorithms, and enhanced mechanical designs have contributed to these advancements. These developments allow robots to manipulate objects with human-like finesse, opening new possibilities in industries like manufacturing, healthcare, and logistics. The integration of tactile feedback and real-time data processing further enhances their ability to interact with dynamic environments. As these technologies continue to evolve, they promise to revolutionize automation, making robots more versatile and efficient in a wide range of applications.
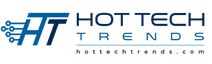