In the rapidly evolving landscape of modern manufacturing, companies are increasingly turning to ready-made components as a strategic choice to enhance efficiency, reduce costs, and accelerate time-to-market. This shift is driven by the need to remain competitive in an industry characterized by rapid technological advancements and ever-changing consumer demands. Ready-made components offer manufacturers the advantage of leveraging pre-designed, tested, and standardized parts, which can significantly streamline production processes. By integrating these components into their operations, manufacturers can focus more on innovation and customization, rather than expending resources on developing every part from scratch. This approach not only reduces the complexity of supply chains but also allows for greater flexibility and scalability in production, enabling manufacturers to respond swiftly to market trends and customer needs. As a result, the adoption of ready-made components is becoming a pivotal strategy for manufacturers aiming to optimize their operations and maintain a competitive edge in the global market.
Cost Efficiency in Using Ready-Made Components
In the ever-evolving landscape of manufacturing, companies are constantly seeking ways to enhance efficiency and reduce costs. One significant trend that has emerged in recent years is the increasing preference for ready-made components. This shift is largely driven by the need for cost efficiency, which is a critical factor in maintaining competitiveness in the global market. By opting for ready-made components, manufacturers can streamline their production processes, reduce overheads, and ultimately deliver products to market more swiftly and economically.
To begin with, the use of ready-made components allows manufacturers to significantly cut down on production time. In traditional manufacturing, the process of designing, prototyping, and producing custom components can be both time-consuming and resource-intensive. By contrast, ready-made components are readily available and can be integrated into the production line with minimal delay. This not only accelerates the manufacturing process but also enables companies to respond more quickly to market demands and changes in consumer preferences. Consequently, manufacturers can maintain a competitive edge by being more agile and responsive.
Moreover, the adoption of ready-made components can lead to substantial cost savings. Custom manufacturing often requires specialized machinery, skilled labor, and extensive quality control measures, all of which contribute to higher production costs. Ready-made components, on the other hand, are typically mass-produced, benefiting from economies of scale. This results in lower per-unit costs, which can be passed on to consumers in the form of more affordable products. Additionally, by reducing the need for specialized equipment and labor, manufacturers can allocate resources more efficiently, focusing on core competencies and innovation rather than component production.
Another important aspect to consider is the quality and reliability of ready-made components. Established suppliers of these components often adhere to stringent quality standards and have extensive experience in their production. This ensures that the components meet industry specifications and perform reliably in their intended applications. By sourcing components from reputable suppliers, manufacturers can mitigate the risks associated with quality control and reduce the likelihood of defects or failures in their final products. This not only enhances the overall quality of the products but also minimizes the costs associated with returns, repairs, and warranty claims.
Furthermore, the use of ready-made components can facilitate greater flexibility in product design and development. Manufacturers can choose from a wide range of components that are compatible with various systems and technologies, allowing for more innovative and customizable product offerings. This flexibility can be particularly advantageous in industries where technological advancements and consumer preferences are rapidly evolving. By incorporating ready-made components, manufacturers can quickly adapt their products to incorporate the latest features and functionalities, thereby meeting the ever-changing demands of the market.
In conclusion, the shift towards ready-made components in manufacturing is primarily driven by the pursuit of cost efficiency. By reducing production time, lowering costs, ensuring quality, and enhancing flexibility, ready-made components offer a compelling solution for manufacturers seeking to optimize their operations. As the manufacturing landscape continues to evolve, it is likely that the adoption of ready-made components will become increasingly prevalent, enabling companies to remain competitive and responsive in a dynamic global market.
Speeding Up Production with Pre-Fabricated Parts
In the ever-evolving landscape of manufacturing, companies are constantly seeking ways to enhance efficiency and reduce production times. One significant trend that has emerged in recent years is the increasing reliance on ready-made components. This shift towards pre-fabricated parts is driven by several factors, each contributing to the overarching goal of speeding up production processes. As manufacturers strive to meet growing consumer demands and maintain a competitive edge, the adoption of ready-made components has become a strategic choice.
To begin with, the use of pre-fabricated parts significantly reduces the time required for production. By sourcing components that are already manufactured to precise specifications, companies can bypass the lengthy and often complex process of creating these parts in-house. This not only accelerates the assembly line but also allows manufacturers to focus their resources on other critical aspects of production, such as quality control and innovation. Consequently, the overall production cycle is shortened, enabling companies to bring their products to market more swiftly.
Moreover, the integration of ready-made components into manufacturing processes enhances consistency and quality. Pre-fabricated parts are typically produced by specialized suppliers who possess the expertise and equipment necessary to ensure high standards. This specialization results in components that are uniform and reliable, reducing the likelihood of defects and inconsistencies in the final product. As a result, manufacturers can maintain a higher level of quality assurance, which is crucial in industries where precision and reliability are paramount.
In addition to improving speed and quality, the use of ready-made components offers significant cost advantages. By outsourcing the production of certain parts, manufacturers can achieve economies of scale that would be difficult to replicate internally. Suppliers of pre-fabricated components often produce in large volumes, allowing them to spread costs over a greater number of units and offer competitive pricing. This cost efficiency is particularly beneficial for small to medium-sized enterprises that may lack the resources to invest in specialized machinery or processes.
Furthermore, the adoption of ready-made components facilitates greater flexibility in production. Manufacturers can quickly adapt to changes in demand or design by sourcing different components as needed. This agility is especially valuable in today’s fast-paced market environment, where consumer preferences and technological advancements can shift rapidly. By having access to a diverse range of pre-fabricated parts, companies can respond more effectively to these changes, ensuring that they remain relevant and competitive.
Another compelling reason for the shift towards ready-made components is the reduction of supply chain complexities. By relying on specialized suppliers, manufacturers can streamline their supply chains, reducing the number of variables and potential points of failure. This simplification not only minimizes the risk of delays but also enhances the overall resilience of the production process. In an era where supply chain disruptions can have significant repercussions, this added reliability is a valuable asset.
In conclusion, the trend of opting for ready-made components is reshaping the manufacturing industry by offering a multitude of benefits. From accelerating production times and improving quality to reducing costs and enhancing flexibility, the advantages are clear. As manufacturers continue to navigate the challenges of a dynamic market, the strategic use of pre-fabricated parts is likely to remain a key factor in achieving operational excellence and sustaining growth.
Enhancing Product Quality Through Standardized Components
In the ever-evolving landscape of manufacturing, companies are increasingly turning to ready-made components as a means to enhance product quality. This shift is driven by a multitude of factors, each contributing to the overarching goal of producing superior products while maintaining efficiency and cost-effectiveness. As manufacturers strive to meet the growing demands of consumers for high-quality goods, the adoption of standardized components has emerged as a strategic approach to achieving these objectives.
One of the primary reasons manufacturers are opting for ready-made components is the assurance of consistent quality. Standardized components are produced under stringent quality control measures, ensuring that each piece meets specific industry standards. This consistency is crucial in maintaining the overall quality of the final product. By integrating components that have been rigorously tested and certified, manufacturers can significantly reduce the risk of defects and malfunctions, thereby enhancing the reliability and durability of their products.
Moreover, the use of ready-made components allows manufacturers to streamline their production processes. By incorporating standardized parts, companies can simplify assembly lines, reduce the complexity of manufacturing operations, and minimize the need for specialized labor. This not only accelerates production timelines but also reduces the likelihood of errors during assembly. Consequently, manufacturers can achieve higher levels of efficiency, which translates into cost savings and increased competitiveness in the market.
In addition to improving efficiency, the adoption of ready-made components facilitates innovation and flexibility in product design. With a wide array of standardized parts available, manufacturers have the freedom to experiment with different configurations and designs without the constraints of custom-made components. This flexibility enables companies to respond swiftly to changing market trends and consumer preferences, thereby maintaining a competitive edge. Furthermore, the ability to quickly adapt to new technologies and integrate them into existing products is a significant advantage in today’s fast-paced market environment.
Another compelling reason for the shift towards ready-made components is the potential for cost reduction. Custom manufacturing of components can be an expensive and time-consuming process, often requiring significant investment in specialized machinery and skilled labor. In contrast, purchasing standardized components in bulk can lead to substantial cost savings due to economies of scale. These savings can then be passed on to consumers in the form of more affordable products, thereby enhancing the manufacturer’s market position.
Furthermore, the use of ready-made components contributes to sustainability efforts within the manufacturing industry. By reducing the need for custom production, manufacturers can decrease their environmental footprint through lower energy consumption and reduced waste generation. Standardized components are often designed with sustainability in mind, utilizing materials and processes that minimize environmental impact. This alignment with sustainable practices not only benefits the environment but also enhances the manufacturer’s reputation as a socially responsible entity.
In conclusion, the trend towards using ready-made components in manufacturing is driven by the desire to enhance product quality while achieving operational efficiency and cost-effectiveness. The consistency, reliability, and flexibility offered by standardized components provide manufacturers with the tools needed to meet consumer demands and adapt to an ever-changing market landscape. As the industry continues to evolve, the adoption of ready-made components is likely to play an increasingly pivotal role in shaping the future of manufacturing, ensuring that companies remain competitive and capable of delivering high-quality products to consumers worldwide.
Reducing Supply Chain Complexity with Ready-Made Solutions
In the ever-evolving landscape of global manufacturing, companies are increasingly seeking ways to streamline operations and enhance efficiency. One significant trend that has emerged in recent years is the shift towards utilizing ready-made components. This approach is gaining traction as manufacturers aim to reduce supply chain complexity, minimize costs, and accelerate time-to-market. By opting for pre-fabricated parts, manufacturers can focus on their core competencies while leveraging the expertise of specialized suppliers.
The decision to incorporate ready-made components into manufacturing processes is driven by several compelling factors. First and foremost, it simplifies the supply chain. Traditionally, manufacturers would source raw materials and produce components in-house, a process that often involves multiple stages and intricate logistics. By contrast, ready-made components are sourced from suppliers who specialize in their production, thereby reducing the number of steps involved in the supply chain. This simplification not only decreases the potential for delays and disruptions but also allows manufacturers to allocate resources more efficiently.
Moreover, the use of ready-made components can lead to significant cost savings. Producing components in-house requires substantial investment in machinery, labor, and raw materials. By purchasing pre-fabricated parts, manufacturers can avoid these expenses and instead benefit from the economies of scale achieved by specialized suppliers. These suppliers often produce components in large volumes, allowing them to offer competitive pricing that individual manufacturers would struggle to match. Consequently, manufacturers can reduce their production costs and improve their overall profitability.
In addition to cost savings, ready-made components offer the advantage of faster time-to-market. In today’s fast-paced business environment, the ability to quickly respond to market demands is crucial. By utilizing pre-fabricated parts, manufacturers can significantly reduce the time required for product development and production. This agility enables companies to capitalize on emerging trends and consumer preferences, thereby gaining a competitive edge in the marketplace. Furthermore, the reduced lead times associated with ready-made components allow manufacturers to better manage inventory levels and respond more effectively to fluctuations in demand.
Another important consideration is the quality and reliability of ready-made components. Specialized suppliers often possess extensive expertise and experience in producing specific parts, ensuring that they meet stringent quality standards. By partnering with reputable suppliers, manufacturers can be confident in the consistency and performance of the components they incorporate into their products. This reliability is particularly crucial in industries where precision and durability are paramount, such as automotive and aerospace manufacturing.
While the benefits of ready-made components are clear, it is essential for manufacturers to carefully evaluate potential suppliers. Establishing strong partnerships with reliable suppliers is critical to ensuring a steady supply of high-quality components. Manufacturers must conduct thorough due diligence, assessing factors such as the supplier’s production capacity, quality control processes, and track record. By doing so, they can mitigate risks and build a resilient supply chain that supports their long-term objectives.
In conclusion, the adoption of ready-made components represents a strategic shift for manufacturers seeking to reduce supply chain complexity and enhance operational efficiency. By simplifying logistics, lowering costs, accelerating time-to-market, and ensuring quality, ready-made solutions offer a compelling value proposition. As the manufacturing landscape continues to evolve, it is likely that more companies will embrace this approach, leveraging the expertise of specialized suppliers to drive innovation and growth.
Leveraging Technological Advancements in Component Manufacturing
In recent years, the manufacturing industry has witnessed a significant shift towards the utilization of ready-made components, a trend largely driven by technological advancements in component manufacturing. This evolution is reshaping the landscape of production processes, offering manufacturers a myriad of benefits that are too compelling to ignore. As technology continues to advance, the precision and quality of ready-made components have reached unprecedented levels, making them an attractive option for manufacturers seeking efficiency and cost-effectiveness.
One of the primary reasons manufacturers are gravitating towards ready-made components is the remarkable improvement in quality control facilitated by modern technology. Advanced manufacturing techniques, such as computer numerical control (CNC) machining and 3D printing, have enabled the production of components with exceptional precision and consistency. These technologies ensure that each component meets stringent quality standards, reducing the likelihood of defects and enhancing the overall reliability of the final product. Consequently, manufacturers can focus on their core competencies, confident in the knowledge that the components they are using are of the highest quality.
Moreover, the adoption of ready-made components significantly reduces production lead times. In a competitive market where time-to-market is crucial, manufacturers are under constant pressure to accelerate their production cycles. By leveraging ready-made components, companies can bypass the time-consuming processes of designing and fabricating individual parts. This not only speeds up production but also allows manufacturers to respond more swiftly to market demands and changes in consumer preferences. As a result, businesses can maintain a competitive edge by delivering products to market faster than ever before.
In addition to time savings, cost efficiency is another compelling factor driving the shift towards ready-made components. The economies of scale achieved through mass production of these components result in lower costs per unit, which can be passed on to manufacturers. This cost advantage is particularly beneficial for small and medium-sized enterprises (SMEs) that may lack the resources to invest in expensive machinery and skilled labor for in-house component production. By outsourcing component manufacturing, SMEs can allocate their resources more effectively, focusing on innovation and product development rather than production logistics.
Furthermore, the integration of ready-made components into manufacturing processes promotes sustainability and environmental responsibility. The precision and efficiency of modern manufacturing technologies minimize material waste, reducing the environmental footprint of production activities. Additionally, many suppliers of ready-made components are adopting sustainable practices, such as using recycled materials and implementing energy-efficient production methods. By choosing these components, manufacturers can align themselves with global sustainability goals and enhance their corporate social responsibility initiatives.
As the manufacturing industry continues to evolve, the role of ready-made components is likely to expand further. The ongoing advancements in technology, such as artificial intelligence and the Internet of Things, are expected to enhance the capabilities of component manufacturing even more. These innovations will likely lead to the development of smarter, more adaptable components that can seamlessly integrate into a wide range of products and systems. Consequently, manufacturers will have even greater opportunities to optimize their production processes and deliver high-quality products to consumers.
In conclusion, the trend towards ready-made components in manufacturing is a testament to the transformative power of technological advancements. By embracing these components, manufacturers can achieve superior quality, reduced lead times, cost efficiency, and sustainability. As technology continues to advance, the benefits of ready-made components will only become more pronounced, solidifying their place as a cornerstone of modern manufacturing strategies.
Sustainability Benefits of Using Ready-Made Components
In recent years, the manufacturing industry has witnessed a significant shift towards the adoption of ready-made components, a trend driven by a multitude of factors, with sustainability emerging as a paramount consideration. As environmental concerns continue to escalate, manufacturers are increasingly recognizing the sustainability benefits associated with utilizing pre-fabricated components. This approach not only aligns with global sustainability goals but also offers practical advantages that contribute to a more efficient and eco-friendly manufacturing process.
To begin with, the use of ready-made components significantly reduces material waste, a critical aspect of sustainable manufacturing. Traditional manufacturing processes often involve cutting and shaping raw materials, which can result in substantial waste. In contrast, ready-made components are produced with precision, minimizing excess material and thereby reducing the overall environmental footprint. This reduction in waste not only conserves resources but also decreases the energy required for waste management and disposal, further enhancing the sustainability of the manufacturing process.
Moreover, the production of ready-made components is typically centralized, allowing for more efficient use of resources and energy. Centralized production facilities can optimize their processes to achieve economies of scale, which translates into lower energy consumption per unit produced. This efficiency is particularly beneficial in reducing greenhouse gas emissions, a major contributor to climate change. By sourcing components from specialized manufacturers, companies can leverage these efficiencies, thereby contributing to a reduction in their overall carbon footprint.
In addition to reducing waste and energy consumption, ready-made components also facilitate the implementation of sustainable supply chain practices. By relying on standardized components, manufacturers can streamline their supply chains, reducing the need for complex logistics and transportation. This simplification not only lowers transportation-related emissions but also enhances the resilience of supply chains, making them less susceptible to disruptions. Consequently, manufacturers can achieve a more sustainable and reliable production process, which is increasingly important in a world where supply chain stability is often challenged by global events.
Furthermore, the adoption of ready-made components supports the principles of a circular economy, an economic system aimed at minimizing waste and making the most of resources. Ready-made components are often designed for durability and reusability, allowing manufacturers to extend the lifecycle of their products. This focus on longevity reduces the need for frequent replacements and repairs, thereby conserving resources and reducing waste. Additionally, when products reach the end of their life, components can often be recovered and repurposed, further contributing to a circular economy model.
Finally, the shift towards ready-made components aligns with consumer expectations and regulatory pressures for more sustainable products. As consumers become more environmentally conscious, they are increasingly demanding products that are produced sustainably. Manufacturers that adopt ready-made components can more easily meet these expectations, enhancing their brand reputation and competitiveness in the market. Simultaneously, regulatory bodies are imposing stricter environmental standards, and the use of ready-made components can help manufacturers comply with these regulations more efficiently.
In conclusion, the sustainability benefits of using ready-made components are manifold, encompassing waste reduction, energy efficiency, supply chain optimization, support for a circular economy, and alignment with consumer and regulatory demands. As manufacturers continue to prioritize sustainability, the adoption of ready-made components is likely to become an integral part of their strategies, driving the industry towards a more sustainable future.
Q&A
1. **Question:** Why do manufacturers choose ready-made components to reduce production time?
**Answer:** Manufacturers opt for ready-made components to significantly cut down on production time, as these components are pre-fabricated and readily available, allowing for faster assembly and quicker time-to-market.
2. **Question:** How do ready-made components impact cost efficiency for manufacturers?
**Answer:** Ready-made components help manufacturers achieve cost efficiency by reducing the need for in-house production facilities and labor, minimizing material waste, and benefiting from economies of scale offered by component suppliers.
3. **Question:** In what way do ready-made components enhance product quality?
**Answer:** Ready-made components often come from specialized suppliers with expertise in their production, ensuring high-quality standards and consistency, which can enhance the overall quality of the final product.
4. **Question:** How do ready-made components contribute to innovation in manufacturing?
**Answer:** By using ready-made components, manufacturers can focus more on design and innovation, leveraging existing technologies and components to create new and improved products without starting from scratch.
5. **Question:** What role do ready-made components play in supply chain management?
**Answer:** Ready-made components simplify supply chain management by reducing the complexity of sourcing raw materials and managing multiple suppliers, leading to more streamlined operations and reduced risk of supply chain disruptions.
6. **Question:** Why might manufacturers prefer ready-made components for scalability?
**Answer:** Manufacturers prefer ready-made components for scalability because they allow for easy adjustments in production volume without the need for significant changes in manufacturing processes or infrastructure, facilitating rapid response to market demand changes.Manufacturers are increasingly opting for ready-made components due to several compelling reasons. Firstly, these components significantly reduce production time, allowing manufacturers to accelerate their time-to-market and respond swiftly to consumer demands. Secondly, ready-made components often come with assured quality and reliability, as they are produced by specialized suppliers with expertise and advanced technology. This reduces the risk of defects and enhances the overall quality of the final product. Additionally, using ready-made components can lead to cost savings, as manufacturers can avoid the expenses associated with developing and producing these parts in-house. This approach also allows manufacturers to focus their resources and expertise on core competencies and innovation, rather than on the complexities of component production. Furthermore, the availability of a wide range of standardized components facilitates greater flexibility and scalability in manufacturing processes, enabling companies to adapt to changing market conditions and customize products to meet specific customer needs. Overall, the strategic use of ready-made components is a practical and efficient solution that supports manufacturers in achieving operational efficiency, cost-effectiveness, and competitive advantage in a dynamic market environment.
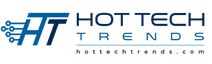