Robotics and automation in manufacturing represent a transformative force reshaping the industrial landscape. These technologies integrate advanced machinery and intelligent systems to enhance production efficiency, precision, and flexibility. Robotics involves the use of programmable machines capable of performing complex tasks with high accuracy, often surpassing human capabilities in speed and endurance. Automation encompasses the broader application of technology to control and monitor production processes, reducing the need for human intervention. Together, they drive significant improvements in productivity, quality, and safety, enabling manufacturers to meet the demands of a competitive global market. By minimizing errors and optimizing resource utilization, robotics and automation facilitate the creation of smart factories, where interconnected systems and data-driven insights lead to continuous improvement and innovation. As these technologies evolve, they promise to further revolutionize manufacturing, paving the way for new business models and opportunities.
The Future Of Robotics In Manufacturing: Trends And Innovations
The future of robotics in manufacturing is poised for transformative advancements, driven by rapid technological innovations and an increasing demand for efficiency and precision. As industries strive to enhance productivity while minimizing costs, the integration of robotics and automation has become a pivotal strategy. This evolution is not merely about replacing human labor but augmenting it, creating a symbiotic relationship between humans and machines that promises to redefine manufacturing processes.
One of the most significant trends in this domain is the development of collaborative robots, or cobots. Unlike traditional industrial robots, which often require isolation from human workers due to safety concerns, cobots are designed to work alongside humans. They are equipped with advanced sensors and machine learning algorithms that enable them to adapt to human actions and ensure safety. This collaboration allows for a more flexible manufacturing environment, where human creativity and machine precision can coexist, leading to enhanced productivity and innovation.
Moreover, the integration of artificial intelligence (AI) in robotics is revolutionizing the manufacturing landscape. AI-powered robots are capable of learning from their environment and improving their performance over time. This adaptability is crucial in a rapidly changing market where customization and quick turnaround times are increasingly important. By leveraging AI, manufacturers can optimize production lines, predict maintenance needs, and reduce downtime, thereby increasing overall efficiency.
In addition to AI, the Internet of Things (IoT) is playing a crucial role in the advancement of robotics in manufacturing. IoT enables the seamless connection of devices and systems, allowing for real-time data collection and analysis. This connectivity facilitates smarter decision-making and enhances the ability to monitor and control manufacturing processes remotely. As a result, manufacturers can achieve greater precision and quality control, which are essential in maintaining competitive advantage.
Another noteworthy innovation is the use of additive manufacturing, commonly known as 3D printing, in conjunction with robotics. This combination allows for the creation of complex and customized components with unprecedented speed and accuracy. By integrating 3D printing capabilities into robotic systems, manufacturers can reduce material waste and lower production costs, while also expanding the possibilities for product design and development.
Furthermore, advancements in machine vision technology are enhancing the capabilities of robotic systems. Machine vision allows robots to interpret visual information from the environment, enabling them to perform tasks that require a high level of precision, such as quality inspection and assembly. This technology is particularly beneficial in industries where accuracy is paramount, such as electronics and automotive manufacturing.
As these trends and innovations continue to evolve, the role of robotics in manufacturing will undoubtedly expand. However, this growth also presents challenges, particularly in terms of workforce adaptation and skills development. As automation becomes more prevalent, there is a pressing need for workers to acquire new skills that complement robotic systems. This shift necessitates investment in education and training programs to ensure that the workforce is equipped to thrive in an increasingly automated environment.
In conclusion, the future of robotics in manufacturing is characterized by a dynamic interplay of technological advancements and human ingenuity. As collaborative robots, AI, IoT, additive manufacturing, and machine vision continue to advance, they will drive significant changes in manufacturing processes. These innovations promise to enhance efficiency, precision, and flexibility, ultimately reshaping the manufacturing industry and paving the way for a new era of industrial productivity.
How Automation Is Revolutionizing The Manufacturing Industry
The manufacturing industry has long been a cornerstone of economic development, driving innovation and providing employment across the globe. In recent years, the integration of robotics and automation has revolutionized this sector, transforming traditional manufacturing processes and setting new standards for efficiency and productivity. As we delve into the impact of automation on manufacturing, it becomes evident that this technological evolution is not merely a trend but a fundamental shift in how goods are produced.
To begin with, the adoption of robotics in manufacturing has significantly enhanced precision and consistency in production. Unlike human workers, robots are capable of performing repetitive tasks with unparalleled accuracy, reducing the likelihood of errors and ensuring uniformity in the final product. This level of precision is particularly crucial in industries such as automotive and electronics, where even minor deviations can lead to significant quality issues. Consequently, manufacturers are increasingly relying on robotic systems to maintain high standards and meet the stringent demands of global markets.
Moreover, automation has drastically improved the efficiency of manufacturing operations. By streamlining processes and minimizing downtime, automated systems enable manufacturers to increase output without compromising on quality. For instance, automated assembly lines can operate continuously, 24/7, without the need for breaks or shift changes, thereby maximizing productivity. This capability is especially beneficial in meeting the growing consumer demand for faster production and delivery times. As a result, companies that embrace automation are better positioned to compete in an increasingly fast-paced and competitive market.
In addition to enhancing efficiency, automation also plays a pivotal role in reducing operational costs. While the initial investment in robotic systems can be substantial, the long-term savings are significant. Automated systems reduce the need for manual labor, thereby lowering labor costs and minimizing the risk of human-related accidents and injuries. Furthermore, robots are capable of operating in hazardous environments, reducing the need for costly safety measures and ensuring a safer workplace for human employees. These cost-saving benefits make automation an attractive option for manufacturers seeking to optimize their operations and improve their bottom line.
Another critical aspect of automation in manufacturing is its ability to facilitate innovation and adaptability. In an era where consumer preferences and market demands are constantly evolving, manufacturers must be agile and responsive to change. Automated systems offer the flexibility to quickly reconfigure production lines and adapt to new product designs or variations. This adaptability not only accelerates the time-to-market for new products but also allows manufacturers to experiment with innovative ideas and processes without significant disruptions.
Despite the numerous advantages, the integration of robotics and automation in manufacturing is not without challenges. Concerns about job displacement and the need for a skilled workforce to manage and maintain automated systems are prevalent. However, it is essential to recognize that automation also creates new opportunities for employment, particularly in areas such as robotics maintenance, programming, and system design. By investing in workforce training and development, manufacturers can ensure a smooth transition to automated processes while equipping their employees with the skills needed for the future.
In conclusion, the impact of robotics and automation on the manufacturing industry is profound and far-reaching. By enhancing precision, efficiency, and adaptability, automation is reshaping the way goods are produced and setting new benchmarks for the industry. As manufacturers continue to embrace these technologies, they are not only improving their operations but also paving the way for a more innovative and sustainable future.
The Role Of Artificial Intelligence In Manufacturing Automation
Artificial intelligence (AI) has become a pivotal force in transforming the landscape of manufacturing automation. As industries strive for greater efficiency and productivity, AI technologies are increasingly being integrated into manufacturing processes, offering unprecedented opportunities for innovation and optimization. The role of AI in manufacturing automation is multifaceted, encompassing various aspects such as predictive maintenance, quality control, supply chain management, and human-robot collaboration.
To begin with, predictive maintenance is one of the most significant applications of AI in manufacturing. By leveraging machine learning algorithms, manufacturers can analyze data from sensors embedded in machinery to predict potential failures before they occur. This proactive approach not only minimizes downtime but also extends the lifespan of equipment, leading to substantial cost savings. Furthermore, AI-driven predictive maintenance allows for more efficient scheduling of maintenance activities, ensuring that resources are allocated optimally and production schedules remain uninterrupted.
In addition to predictive maintenance, AI plays a crucial role in enhancing quality control processes. Traditional quality control methods often rely on manual inspections, which can be time-consuming and prone to human error. AI-powered vision systems, however, can rapidly analyze products on the production line, identifying defects with remarkable accuracy. These systems utilize deep learning algorithms to recognize patterns and anomalies, ensuring that only products meeting the highest standards reach the market. Consequently, manufacturers can maintain consistent quality while reducing waste and rework.
Moreover, AI is revolutionizing supply chain management by providing manufacturers with real-time insights and predictive analytics. By analyzing vast amounts of data from various sources, AI systems can forecast demand, optimize inventory levels, and streamline logistics operations. This level of insight enables manufacturers to respond swiftly to market changes, reducing lead times and improving customer satisfaction. Additionally, AI can identify potential disruptions in the supply chain, allowing companies to mitigate risks and maintain continuity in their operations.
Another critical aspect of AI in manufacturing automation is the facilitation of human-robot collaboration. As robots become more intelligent and capable, they are increasingly working alongside human operators on the factory floor. AI enables robots to learn from their human counterparts, adapting to new tasks and environments with ease. This collaboration not only enhances productivity but also allows humans to focus on more complex and creative tasks, thereby fostering innovation. Furthermore, AI-driven robots can improve workplace safety by taking on hazardous tasks, reducing the risk of injury to human workers.
Despite the numerous advantages of AI in manufacturing automation, it is essential to address the challenges associated with its implementation. Data privacy and security concerns must be carefully managed, as the integration of AI systems often involves the collection and analysis of sensitive information. Additionally, the workforce must be adequately trained to work with AI technologies, necessitating investment in education and skill development.
In conclusion, the role of artificial intelligence in manufacturing automation is transformative, offering significant benefits in terms of efficiency, quality, and innovation. As AI technologies continue to evolve, their integration into manufacturing processes will undoubtedly become more sophisticated, driving further advancements in the industry. By embracing AI, manufacturers can not only enhance their competitive edge but also contribute to a more sustainable and resilient industrial landscape.
Benefits Of Implementing Robotics In Manufacturing Processes
The integration of robotics and automation in manufacturing processes has revolutionized the industrial landscape, offering a multitude of benefits that enhance efficiency, precision, and productivity. As industries strive to remain competitive in an increasingly globalized market, the adoption of robotic technologies has become a pivotal strategy. One of the most significant advantages of implementing robotics in manufacturing is the substantial increase in productivity. Robots are capable of operating continuously without fatigue, unlike their human counterparts, which allows for uninterrupted production cycles. This continuous operation not only maximizes output but also reduces the time required to bring products to market, thereby providing a competitive edge.
Moreover, the precision and consistency offered by robotic systems are unparalleled. Human error, which can lead to defects and inconsistencies, is significantly minimized when robots are employed. This precision is particularly crucial in industries where even the slightest deviation can result in substantial financial losses or safety hazards. For instance, in the automotive and aerospace sectors, the accuracy of robotic systems ensures that components are assembled with exacting standards, thereby enhancing the overall quality and reliability of the final product.
In addition to improving quality and productivity, robotics and automation contribute to enhanced workplace safety. Manufacturing environments often involve hazardous tasks that pose risks to human workers, such as handling heavy materials or working in extreme temperatures. By delegating these dangerous tasks to robots, companies can significantly reduce the incidence of workplace injuries, thereby fostering a safer working environment. This not only protects the workforce but also reduces costs associated with workplace accidents, such as medical expenses and compensation claims.
Furthermore, the flexibility offered by modern robotic systems is a noteworthy benefit. Advanced robotics can be programmed and reprogrammed to perform a wide array of tasks, allowing manufacturers to quickly adapt to changing production needs or market demands. This adaptability is particularly advantageous in industries characterized by rapid product cycles or customization requirements. By swiftly adjusting to new specifications, manufacturers can maintain their responsiveness to consumer demands without incurring significant downtime or retooling costs.
The implementation of robotics also leads to cost savings in the long term. While the initial investment in robotic systems can be substantial, the reduction in labor costs, coupled with increased efficiency and reduced waste, often results in a favorable return on investment. Additionally, robots can work in environments that are not conducive to human labor, such as cleanrooms or areas with hazardous materials, further expanding the scope of manufacturing capabilities without incurring additional costs for specialized human labor.
Moreover, the data collection and analysis capabilities of robotic systems provide manufacturers with valuable insights into their operations. By monitoring production processes in real-time, companies can identify bottlenecks, optimize workflows, and implement predictive maintenance strategies to prevent equipment failures. This data-driven approach not only enhances operational efficiency but also supports informed decision-making, enabling manufacturers to continuously improve their processes and maintain a competitive advantage.
In conclusion, the benefits of implementing robotics in manufacturing processes are manifold, encompassing increased productivity, precision, safety, flexibility, cost savings, and data-driven insights. As technology continues to advance, the role of robotics in manufacturing is poised to expand further, driving innovation and efficiency across industries. Embracing these technologies is not merely an option but a necessity for manufacturers seeking to thrive in the modern industrial landscape.
Overcoming Challenges In Robotics And Automation Integration
The integration of robotics and automation in manufacturing has revolutionized the industry, offering unprecedented levels of efficiency, precision, and productivity. However, despite these advantages, the journey toward full integration is fraught with challenges that manufacturers must navigate carefully. Understanding these challenges and developing strategies to overcome them is crucial for businesses aiming to remain competitive in an increasingly automated world.
One of the primary challenges in integrating robotics and automation is the significant initial investment required. The cost of acquiring advanced robotic systems, coupled with the expenses associated with installation and maintenance, can be prohibitive for many manufacturers, particularly small and medium-sized enterprises. To address this, companies can explore various financing options, such as leasing or partnering with technology providers, to mitigate the financial burden. Additionally, government incentives and grants aimed at promoting technological advancement can provide much-needed support.
Another critical challenge is the need for a skilled workforce capable of operating and maintaining these sophisticated systems. The shift towards automation necessitates a workforce with expertise in robotics, programming, and systems integration. Consequently, manufacturers must invest in training and upskilling their employees to ensure they possess the necessary competencies. Collaborating with educational institutions to develop specialized training programs can also help bridge the skills gap, ensuring a steady pipeline of qualified personnel.
Moreover, the integration of robotics and automation often requires significant changes to existing manufacturing processes. This can lead to disruptions and downtime, which may impact productivity and profitability. To minimize these disruptions, manufacturers should adopt a phased approach to integration, allowing for gradual adaptation and minimizing the risk of operational setbacks. Conducting thorough assessments and simulations before implementation can also help identify potential bottlenecks and streamline the transition process.
Interoperability between new robotic systems and existing machinery is another challenge that manufacturers must address. Ensuring seamless communication and coordination between different systems is essential for maximizing efficiency and avoiding costly errors. To achieve this, manufacturers should prioritize the adoption of standardized protocols and interfaces that facilitate interoperability. Engaging with industry consortia and participating in collaborative efforts to develop universal standards can further enhance compatibility and integration.
Furthermore, cybersecurity concerns pose a significant challenge in the realm of robotics and automation. As manufacturing systems become increasingly interconnected, they become more vulnerable to cyber threats. Protecting sensitive data and ensuring the integrity of automated processes is paramount. Manufacturers must implement robust cybersecurity measures, including firewalls, encryption, and regular security audits, to safeguard their operations. Additionally, fostering a culture of cybersecurity awareness among employees can help mitigate risks and ensure compliance with best practices.
Finally, the rapid pace of technological advancement presents a challenge in itself. Manufacturers must continuously adapt to new developments and innovations to remain competitive. This requires a commitment to ongoing research and development, as well as a willingness to embrace change. By fostering a culture of innovation and staying abreast of emerging trends, manufacturers can position themselves at the forefront of the industry.
In conclusion, while the integration of robotics and automation in manufacturing presents numerous challenges, these can be effectively managed through strategic planning and proactive measures. By addressing financial constraints, investing in workforce development, ensuring process adaptability, prioritizing interoperability, enhancing cybersecurity, and embracing innovation, manufacturers can successfully navigate the complexities of automation integration. In doing so, they can unlock the full potential of robotics and automation, driving growth and competitiveness in the modern manufacturing landscape.
Case Studies: Successful Automation In Modern Manufacturing
In recent years, the integration of robotics and automation in manufacturing has revolutionized the industry, leading to significant improvements in efficiency, productivity, and quality. Several case studies highlight the successful implementation of these technologies, offering valuable insights into their transformative potential. One notable example is the automotive industry, where companies like Tesla have embraced automation to streamline production processes. By employing advanced robotics, Tesla has managed to reduce assembly time and enhance precision in manufacturing. This has not only increased output but also improved the overall quality of their vehicles, setting a new standard in the industry.
Similarly, the electronics sector has witnessed remarkable advancements through automation. Foxconn, a major supplier for companies like Apple, has implemented robotic systems to handle repetitive tasks such as soldering and assembly. This shift has allowed Foxconn to maintain high production volumes while minimizing human error. Moreover, the use of automation has enabled the company to reallocate human resources to more complex tasks, thereby fostering innovation and skill development among its workforce.
Transitioning to the food and beverage industry, automation has played a crucial role in enhancing operational efficiency. For instance, Coca-Cola has integrated automated systems in its bottling plants to optimize the filling and packaging processes. This has resulted in a significant reduction in production time and waste, while ensuring consistent product quality. The implementation of robotics in these facilities has also improved safety standards by minimizing human exposure to potentially hazardous environments.
In the pharmaceutical industry, automation has been instrumental in ensuring precision and compliance with stringent regulatory standards. Pfizer, a leading pharmaceutical company, has adopted robotic systems for tasks such as drug formulation and packaging. This has not only accelerated production timelines but also enhanced accuracy in dosage and labeling, thereby ensuring patient safety. Furthermore, automation has facilitated real-time monitoring and data collection, enabling Pfizer to maintain rigorous quality control throughout the manufacturing process.
The textile industry, traditionally labor-intensive, has also benefited from automation. Companies like Adidas have introduced robotic systems in their manufacturing units to automate tasks such as cutting and sewing. This has led to a significant reduction in production costs and time, while maintaining high-quality standards. Additionally, automation has allowed Adidas to respond swiftly to market demands, offering customized products with shorter lead times.
Moreover, the aerospace industry has leveraged automation to achieve unprecedented levels of precision and efficiency. Boeing, for example, has integrated robotics in the assembly of aircraft components, such as wings and fuselage sections. This has not only improved the accuracy of assembly but also reduced the time required for production. The use of automation in aerospace manufacturing has also enhanced safety by minimizing human involvement in potentially dangerous tasks.
In conclusion, the successful implementation of robotics and automation across various manufacturing sectors underscores their transformative potential. These technologies have not only improved efficiency and productivity but also enhanced quality and safety standards. As industries continue to evolve, the integration of robotics and automation will undoubtedly play a pivotal role in shaping the future of manufacturing. By learning from these case studies, companies can harness the power of automation to drive innovation and maintain a competitive edge in the global market.
Q&A
1. **What is robotics in manufacturing?**
Robotics in manufacturing involves the use of programmable machines to perform tasks such as assembly, welding, painting, and material handling, enhancing efficiency and precision.
2. **How does automation benefit manufacturing?**
Automation improves manufacturing by increasing production speed, reducing human error, lowering labor costs, and enhancing safety by taking over dangerous tasks.
3. **What are collaborative robots (cobots)?**
Collaborative robots, or cobots, are designed to work alongside humans, assisting with tasks while ensuring safety through advanced sensors and programming.
4. **What is the role of AI in manufacturing automation?**
AI in manufacturing automation optimizes processes through predictive maintenance, quality control, supply chain management, and adaptive production systems.
5. **What are the challenges of implementing robotics in manufacturing?**
Challenges include high initial costs, the need for skilled personnel, integration with existing systems, and potential job displacement concerns.
6. **What is Industry 4.0 in the context of manufacturing?**
Industry 4.0 refers to the integration of digital technologies, such as IoT, AI, and robotics, into manufacturing to create smart, interconnected production systems.Robotics and automation have revolutionized the manufacturing industry by significantly enhancing efficiency, precision, and productivity. The integration of advanced robotic systems and automated processes has led to reduced labor costs, minimized human error, and increased production speed. These technologies enable manufacturers to maintain high-quality standards while adapting to rapidly changing market demands. Furthermore, robotics and automation facilitate the implementation of smart manufacturing practices, such as real-time data analysis and predictive maintenance, which optimize operations and resource management. As the industry continues to evolve, the adoption of robotics and automation is expected to expand, driving innovation and competitiveness in manufacturing.
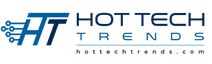