Edge computing is a distributed computing paradigm that brings computation and data storage closer to the location where it is needed, improving response times and saving bandwidth. This approach is particularly beneficial in industrial settings, where real-time data processing and low-latency responses are critical. By processing data at or near the source, edge computing reduces the need to send vast amounts of information to centralized data centers, thus enhancing efficiency and reliability.
In industrial applications, edge computing is transforming operations across various sectors. In manufacturing, it enables predictive maintenance by analyzing data from machinery in real-time, reducing downtime and maintenance costs. In the energy sector, edge computing facilitates smart grid management by processing data from distributed energy resources, optimizing energy distribution, and improving grid reliability. Additionally, in the field of autonomous vehicles, edge computing supports real-time decision-making by processing sensor data locally, ensuring faster and safer navigation. Overall, edge computing is driving innovation and efficiency in industries by enabling faster data processing, enhancing operational capabilities, and supporting the deployment of advanced technologies.
Enhancing Manufacturing Efficiency Through Edge Computing
Edge computing is revolutionizing the manufacturing industry by enhancing efficiency and enabling real-time data processing at the source of data generation. As industries strive to optimize operations and reduce latency, edge computing emerges as a pivotal technology that addresses these needs by processing data closer to where it is generated, rather than relying solely on centralized cloud computing. This shift is particularly significant in manufacturing, where the ability to process data in real-time can lead to substantial improvements in productivity, quality control, and operational efficiency.
One of the primary advantages of edge computing in manufacturing is its ability to reduce latency. In traditional cloud computing models, data must travel from the point of generation to a centralized data center for processing, which can introduce delays. In contrast, edge computing processes data locally, allowing for immediate analysis and decision-making. This is crucial in manufacturing environments where even milliseconds of delay can impact the quality of products or the efficiency of production lines. By minimizing latency, edge computing enables manufacturers to respond swiftly to changes in production conditions, thereby enhancing overall efficiency.
Moreover, edge computing facilitates improved data management and security. In manufacturing, vast amounts of data are generated by machines, sensors, and other devices. Transmitting all this data to a central cloud can be costly and pose security risks. Edge computing addresses these challenges by processing and filtering data locally, ensuring that only relevant information is sent to the cloud for further analysis. This not only reduces bandwidth costs but also enhances data security by minimizing the exposure of sensitive information to potential cyber threats.
In addition to latency reduction and improved data management, edge computing supports predictive maintenance, a critical aspect of modern manufacturing. By analyzing data from machinery and equipment in real-time, edge computing can identify patterns and anomalies that may indicate potential failures. This allows manufacturers to perform maintenance proactively, reducing downtime and extending the lifespan of equipment. Consequently, predictive maintenance enabled by edge computing contributes to significant cost savings and increased operational efficiency.
Furthermore, edge computing enhances quality control processes in manufacturing. By processing data at the edge, manufacturers can conduct real-time quality assessments and detect defects as they occur. This immediate feedback loop allows for quick adjustments to production processes, ensuring that products meet quality standards and reducing waste. The ability to maintain high-quality production standards is essential for manufacturers seeking to remain competitive in a global market.
As the manufacturing industry continues to embrace digital transformation, the integration of edge computing with other emerging technologies, such as the Internet of Things (IoT) and artificial intelligence (AI), is becoming increasingly prevalent. IoT devices generate vast amounts of data that can be processed at the edge, while AI algorithms can be deployed locally to enhance decision-making processes. This synergy between edge computing, IoT, and AI creates a robust framework for smart manufacturing, where data-driven insights drive continuous improvement and innovation.
In conclusion, edge computing is a transformative force in the manufacturing industry, offering numerous benefits that enhance efficiency and productivity. By reducing latency, improving data management, supporting predictive maintenance, and enhancing quality control, edge computing empowers manufacturers to optimize their operations and remain competitive in an ever-evolving landscape. As technology continues to advance, the role of edge computing in manufacturing is poised to expand, driving further innovation and efficiency across the industry.
Real-Time Data Processing in Smart Factories
Edge computing has emerged as a transformative force in the realm of smart factories, offering unprecedented capabilities for real-time data processing. As industries increasingly adopt smart technologies, the need for efficient data management and processing becomes paramount. Edge computing addresses this need by decentralizing data processing, bringing it closer to the source of data generation. This approach significantly reduces latency, enhances data security, and optimizes bandwidth usage, making it an ideal solution for the dynamic environment of smart factories.
In smart factories, the integration of Internet of Things (IoT) devices has led to an exponential increase in data generation. These devices, ranging from sensors to advanced machinery, continuously produce vast amounts of data that require immediate analysis to ensure optimal performance and decision-making. Traditional cloud computing models, which rely on centralized data processing, often struggle to meet the real-time demands of smart factories due to inherent latency issues. This is where edge computing steps in, providing a decentralized architecture that processes data at or near the source, thereby minimizing delays and enabling instantaneous insights.
Moreover, edge computing enhances the reliability and resilience of smart factory operations. By processing data locally, edge devices can continue to function even in the event of network disruptions or connectivity issues. This ensures that critical operations are not hindered by external factors, maintaining the seamless flow of production processes. Additionally, edge computing allows for more efficient use of network resources. By filtering and processing data locally, only relevant information is transmitted to the cloud, reducing the burden on network infrastructure and lowering operational costs.
Another significant advantage of edge computing in smart factories is its contribution to data security and privacy. With data being processed closer to its source, there is a reduced risk of exposure to cyber threats during transmission. This localized processing also allows for the implementation of robust security measures tailored to specific factory environments, further safeguarding sensitive information. As industries become more data-driven, ensuring the security and integrity of data is crucial, and edge computing provides a viable solution to these challenges.
Furthermore, edge computing facilitates advanced analytics and machine learning applications within smart factories. By enabling real-time data processing, edge devices can support complex algorithms and models that require immediate feedback. This capability is particularly beneficial for predictive maintenance, quality control, and process optimization. For instance, edge computing can analyze sensor data from machinery to predict potential failures before they occur, allowing for timely maintenance and reducing downtime. Similarly, real-time quality control can be achieved by analyzing production data on the fly, ensuring that products meet the required standards without delay.
In conclusion, edge computing plays a pivotal role in the evolution of smart factories by enabling real-time data processing and analysis. Its ability to reduce latency, enhance security, and support advanced analytics makes it an indispensable tool for modern industrial applications. As industries continue to embrace digital transformation, the adoption of edge computing will likely accelerate, driving further innovation and efficiency in smart manufacturing environments. By bringing computation closer to the data source, edge computing not only addresses the challenges of traditional data processing models but also unlocks new possibilities for the future of industrial operations.
Edge Computing for Predictive Maintenance in Industrial Equipment
Edge computing has emerged as a transformative technology in the realm of industrial applications, particularly in the area of predictive maintenance for industrial equipment. As industries strive to enhance operational efficiency and reduce downtime, the integration of edge computing into predictive maintenance strategies offers a promising solution. By processing data closer to the source, edge computing enables real-time analysis and decision-making, which is crucial for maintaining the health and performance of industrial machinery.
In traditional predictive maintenance systems, data collected from sensors on industrial equipment is often sent to centralized cloud servers for analysis. While this approach provides valuable insights, it is not without its limitations. The latency involved in transmitting data to and from the cloud can delay critical maintenance decisions, potentially leading to equipment failures and costly downtime. Furthermore, the sheer volume of data generated by industrial sensors can overwhelm network bandwidth, resulting in inefficiencies and increased operational costs.
Edge computing addresses these challenges by decentralizing data processing. By deploying computing resources at the edge of the network, closer to the equipment itself, data can be analyzed in real-time. This immediate processing capability allows for the rapid detection of anomalies and potential failures, enabling maintenance teams to take proactive measures before issues escalate. Consequently, edge computing enhances the responsiveness of predictive maintenance systems, reducing the risk of unexpected equipment breakdowns and extending the lifespan of machinery.
Moreover, edge computing facilitates the integration of advanced analytics and machine learning algorithms into predictive maintenance strategies. By leveraging the computational power available at the edge, industries can implement sophisticated models that continuously learn from equipment data. These models can identify patterns and trends that may indicate impending failures, providing maintenance teams with actionable insights. As a result, maintenance activities can be scheduled more effectively, minimizing disruptions to production processes and optimizing resource allocation.
In addition to improving the timeliness and accuracy of maintenance decisions, edge computing also enhances data security and privacy. By processing data locally, sensitive information remains within the confines of the industrial facility, reducing the risk of exposure to external threats. This is particularly important in industries where data confidentiality is paramount, such as in manufacturing sectors dealing with proprietary processes or critical infrastructure.
Furthermore, the scalability of edge computing solutions makes them well-suited for diverse industrial environments. Whether in a large-scale manufacturing plant or a remote oil rig, edge computing can be tailored to meet specific operational requirements. This flexibility allows industries to implement predictive maintenance strategies that are both cost-effective and efficient, regardless of the scale or complexity of their operations.
In conclusion, edge computing represents a significant advancement in the field of predictive maintenance for industrial equipment. By enabling real-time data processing and analysis at the source, it addresses the limitations of traditional cloud-based systems, offering improved responsiveness, accuracy, and security. As industries continue to embrace digital transformation, the adoption of edge computing in predictive maintenance strategies is poised to drive significant improvements in operational efficiency and equipment reliability. Through its ability to facilitate timely and informed maintenance decisions, edge computing is set to play a pivotal role in the future of industrial operations.
Improving Supply Chain Management with Edge Technology
Edge computing is revolutionizing various sectors by bringing data processing closer to the source of data generation, thereby reducing latency and improving efficiency. In the realm of supply chain management, this technological advancement is proving to be particularly transformative. As businesses strive to enhance their operational efficiency and responsiveness, edge computing offers a promising solution by enabling real-time data processing and decision-making at the edge of the network.
One of the primary benefits of edge computing in supply chain management is its ability to process data locally, which significantly reduces the time required to analyze and act upon information. This is crucial in supply chain operations, where timely decisions can lead to substantial cost savings and improved service levels. For instance, in a warehouse setting, edge devices can process data from sensors and cameras to monitor inventory levels, track the movement of goods, and optimize storage space. By doing so, businesses can ensure that inventory is managed more efficiently, reducing the risk of overstocking or stockouts.
Moreover, edge computing enhances the visibility and traceability of goods throughout the supply chain. By deploying edge devices at various points along the supply chain, companies can collect and analyze data in real-time, providing them with a comprehensive view of their operations. This real-time visibility allows for better tracking of shipments, improved demand forecasting, and more accurate delivery estimates. Consequently, businesses can respond more swiftly to disruptions, such as delays or changes in demand, thereby maintaining a more resilient supply chain.
In addition to improving operational efficiency, edge computing also plays a critical role in enhancing the security of supply chain operations. With data being processed closer to its source, the risk of data breaches and cyberattacks is reduced, as there is less reliance on centralized data centers. Furthermore, edge devices can employ advanced security protocols to protect sensitive information, ensuring that data integrity is maintained throughout the supply chain. This is particularly important in industries such as pharmaceuticals and food and beverage, where the security and authenticity of products are paramount.
Another significant advantage of edge computing in supply chain management is its ability to support advanced technologies such as the Internet of Things (IoT) and artificial intelligence (AI). By integrating edge computing with IoT devices, businesses can gather and process vast amounts of data from connected devices, enabling more intelligent and automated supply chain operations. For example, AI algorithms can be deployed at the edge to predict equipment failures, optimize routing and scheduling, and enhance quality control processes. This integration not only improves efficiency but also drives innovation, allowing companies to develop new business models and services.
Furthermore, edge computing facilitates greater scalability and flexibility in supply chain operations. As businesses grow and expand their operations, the ability to quickly deploy and manage edge devices allows them to adapt to changing demands and market conditions. This scalability is particularly beneficial for companies operating in dynamic and competitive environments, where the ability to respond rapidly to changes can provide a significant competitive advantage.
In conclusion, edge computing is poised to play a pivotal role in transforming supply chain management by enabling real-time data processing, enhancing visibility and security, and supporting advanced technologies. As businesses continue to seek ways to improve their supply chain operations, the adoption of edge computing will undoubtedly become an integral part of their strategies, driving efficiency, innovation, and resilience in an increasingly complex and interconnected world.
Edge Computing in Industrial IoT: Transforming Operations
Edge computing is rapidly transforming the landscape of industrial operations, particularly within the realm of the Industrial Internet of Things (IIoT). As industries increasingly rely on connected devices to enhance efficiency and productivity, the need for real-time data processing has become paramount. Edge computing addresses this need by bringing computation and data storage closer to the location where it is needed, thereby reducing latency and bandwidth usage. This shift is proving to be a game-changer for industries that require immediate data analysis and decision-making capabilities.
One of the primary advantages of edge computing in industrial settings is its ability to process data locally, which significantly reduces the time it takes to analyze and act upon information. In traditional cloud computing models, data is sent to centralized data centers for processing, which can introduce delays. However, with edge computing, data is processed at or near the source, allowing for faster response times. This is particularly beneficial in industries such as manufacturing, where real-time monitoring and control of machinery are crucial for maintaining operational efficiency and preventing downtime.
Moreover, edge computing enhances the reliability and security of industrial operations. By processing data locally, sensitive information does not need to be transmitted over potentially insecure networks to distant data centers. This localized processing reduces the risk of data breaches and ensures that critical operations can continue even if connectivity to the central cloud is lost. In sectors such as oil and gas, where remote locations are common, the ability to operate independently of a central network is invaluable.
In addition to improving speed and security, edge computing also enables more efficient use of network resources. By filtering and processing data at the edge, only relevant information is sent to the cloud for further analysis or storage. This reduces the amount of data that needs to be transmitted, thereby conserving bandwidth and lowering costs. For industries with extensive sensor networks, such as agriculture or logistics, this efficiency can lead to significant savings and improved operational performance.
Furthermore, edge computing supports the integration of advanced technologies such as artificial intelligence (AI) and machine learning (ML) into industrial processes. By deploying AI and ML algorithms at the edge, industries can leverage real-time data to optimize operations, predict maintenance needs, and enhance decision-making. For instance, in the automotive industry, edge computing can enable autonomous vehicles to process data from sensors and cameras instantaneously, allowing for immediate adjustments to driving conditions.
As industries continue to adopt edge computing, the potential for innovation and improvement in operational processes is vast. The ability to process data in real-time, coupled with enhanced security and efficient resource use, positions edge computing as a critical component of the IIoT ecosystem. As a result, industries are not only able to improve their current operations but also explore new business models and opportunities that were previously unattainable.
In conclusion, edge computing is revolutionizing industrial operations by providing the necessary infrastructure for real-time data processing and decision-making. Its applications across various sectors demonstrate its versatility and effectiveness in addressing the unique challenges faced by industries today. As technology continues to evolve, the role of edge computing in industrial IoT will undoubtedly expand, offering even greater benefits and driving further advancements in industrial efficiency and innovation.
Securing Industrial Networks with Edge Computing Solutions
Edge computing has emerged as a transformative force in the realm of industrial networks, offering a robust solution to the growing demands for enhanced security and efficiency. As industries increasingly rely on interconnected devices and systems, the need for secure, real-time data processing has become paramount. Edge computing addresses these needs by decentralizing data processing, bringing it closer to the source of data generation. This approach not only reduces latency but also enhances the security of industrial networks by minimizing the exposure of sensitive data to potential cyber threats.
In traditional cloud computing models, data is transmitted to centralized data centers for processing, which can introduce vulnerabilities and delays. However, edge computing mitigates these risks by processing data locally at the edge of the network. This localized processing ensures that sensitive information does not need to travel across potentially insecure networks, thereby reducing the risk of interception or unauthorized access. Moreover, by keeping data closer to its source, edge computing allows for faster response times, which is crucial in industrial settings where real-time decision-making is often required.
Furthermore, edge computing enhances the resilience of industrial networks. In the event of a network disruption or failure, edge devices can continue to operate independently, ensuring that critical processes remain uninterrupted. This capability is particularly valuable in industries such as manufacturing, energy, and transportation, where downtime can result in significant financial losses and safety hazards. By maintaining local processing capabilities, edge computing provides a layer of redundancy that bolsters the overall reliability of industrial networks.
In addition to improving security and resilience, edge computing also facilitates the integration of advanced technologies such as artificial intelligence (AI) and machine learning (ML) into industrial operations. By processing data at the edge, these technologies can analyze and act on information in real-time, enabling predictive maintenance, quality control, and process optimization. For instance, in a manufacturing plant, edge devices equipped with AI algorithms can monitor equipment performance and predict potential failures before they occur, thereby reducing downtime and maintenance costs.
Moreover, edge computing supports the scalability of industrial networks. As industries expand and incorporate more devices and sensors, the volume of data generated can overwhelm traditional centralized systems. Edge computing alleviates this burden by distributing processing tasks across multiple edge devices, allowing networks to scale efficiently without compromising performance or security. This scalability is essential for industries looking to harness the full potential of the Internet of Things (IoT) and other emerging technologies.
Despite its numerous advantages, the implementation of edge computing in industrial networks is not without challenges. Ensuring interoperability between diverse edge devices and systems, managing distributed data, and maintaining consistent security protocols across the network are complex tasks that require careful planning and execution. However, with the continued advancement of edge computing technologies and standards, these challenges are being progressively addressed, paving the way for broader adoption across various industrial sectors.
In conclusion, edge computing offers a compelling solution for securing industrial networks by enhancing data security, improving resilience, and enabling real-time processing capabilities. As industries continue to evolve and embrace digital transformation, the role of edge computing in safeguarding and optimizing industrial operations is set to become increasingly significant. By addressing the unique demands of industrial environments, edge computing not only secures networks but also drives innovation and efficiency, ultimately contributing to the advancement of modern industry.
Q&A
1. **What is Edge Computing?**
Edge computing is a distributed computing paradigm that brings computation and data storage closer to the location where it is needed, improving response times and saving bandwidth.
2. **How does Edge Computing benefit industrial applications?**
Edge computing benefits industrial applications by reducing latency, improving real-time data processing, enhancing data security, and enabling more efficient use of network resources.
3. **What are some common industrial applications of Edge Computing?**
Common industrial applications include predictive maintenance, real-time monitoring and control of manufacturing processes, autonomous vehicles, and smart grid management.
4. **How does Edge Computing support predictive maintenance?**
Edge computing supports predictive maintenance by processing data from sensors on machinery locally, allowing for real-time analysis and early detection of potential failures.
5. **What role does Edge Computing play in autonomous vehicles?**
In autonomous vehicles, edge computing processes data from sensors and cameras in real-time, enabling quick decision-making and reducing reliance on cloud-based processing.
6. **How does Edge Computing enhance data security in industrial settings?**
Edge computing enhances data security by processing and storing sensitive data locally, reducing the risk of data breaches during transmission to centralized cloud servers.Edge computing represents a transformative shift in how data is processed, analyzed, and utilized across various industries. By decentralizing data processing and bringing it closer to the source of data generation, edge computing reduces latency, enhances real-time decision-making, and improves bandwidth efficiency. In industrial applications, this technology is pivotal in enabling smart manufacturing, predictive maintenance, and enhanced operational efficiency. It supports the Industrial Internet of Things (IIoT) by facilitating rapid data processing and analysis at the edge, which is crucial for applications requiring immediate feedback and action, such as autonomous vehicles, robotics, and remote monitoring systems. Furthermore, edge computing enhances data security and privacy by minimizing the need to transfer sensitive information to centralized data centers. As industries continue to embrace digital transformation, edge computing will play a critical role in driving innovation, optimizing processes, and creating new business opportunities.
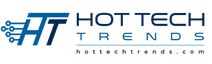