Advanced microsoldering techniques are essential for professionals seeking to excel in the intricate world of electronic repair and manufacturing. On Day Three of mastering these skills, the focus shifts to BGA (Ball Grid Array) reballing, a critical process in the restoration and enhancement of electronic components. BGA reballing involves the meticulous removal and replacement of solder balls on a chip, ensuring optimal connectivity and functionality. This advanced technique requires precision, patience, and a deep understanding of the tools and materials involved. By mastering BGA reballing, technicians can significantly extend the lifespan of electronic devices, improve performance, and reduce waste, making it a vital skill in the ever-evolving field of electronics.
Understanding BGA Reballing: Essential Tools and Equipment
On the third day of mastering BGA reballing, a crucial aspect of advanced microsoldering techniques, it becomes imperative to delve into the essential tools and equipment that facilitate this intricate process. Understanding the nuances of BGA reballing requires not only skill but also the right set of tools to ensure precision and efficiency. As we explore the necessary equipment, it is important to recognize that each tool plays a pivotal role in achieving successful outcomes in BGA reballing.
To begin with, a high-quality soldering station is indispensable. This piece of equipment provides the necessary heat control and stability required for delicate soldering tasks. A soldering station with adjustable temperature settings allows for precise control, which is crucial when working with sensitive components. Moreover, the inclusion of a hot air rework station is equally vital. This tool is used to evenly distribute heat across the BGA component, ensuring that the solder balls melt uniformly during the reballing process. The ability to control airflow and temperature is essential to prevent damage to the component or the PCB.
In addition to soldering stations, a microscope is an essential tool for BGA reballing. Given the minuscule size of BGA components, a microscope provides the magnification necessary to inspect and align the solder balls accurately. This ensures that each ball is correctly positioned, which is critical for the functionality of the reballing process. Furthermore, a stencil printer is another key piece of equipment. This tool aids in the precise application of solder paste onto the BGA pads, ensuring that the solder balls adhere correctly during the reflow process.
Transitioning to the materials required, solder balls themselves are fundamental to BGA reballing. These tiny spheres of solder are available in various sizes and compositions, and selecting the appropriate type is crucial for compatibility with the specific BGA component being worked on. Additionally, solder paste is used in conjunction with the stencil printer to facilitate the attachment of solder balls to the BGA pads. The paste must be of high quality to ensure proper adhesion and reflow characteristics.
Moreover, flux is another critical material in the BGA reballing process. It serves to clean and prepare the surfaces of the BGA pads and solder balls, promoting better solderability and reducing the risk of defects. The choice of flux can significantly impact the quality of the reballing process, making it essential to select a flux that is compatible with the solder balls and the specific requirements of the task at hand.
Finally, it is important to consider the role of cleaning tools in BGA reballing. After the reballing process, any residual flux or solder paste must be meticulously cleaned to prevent corrosion or electrical shorts. Tools such as isopropyl alcohol and lint-free wipes are commonly used to ensure that the BGA component and the surrounding area are free from contaminants.
In conclusion, mastering BGA reballing on day three involves a comprehensive understanding of the essential tools and equipment required for this advanced microsoldering technique. From soldering stations and microscopes to solder balls and cleaning materials, each component plays a vital role in ensuring the precision and success of the reballing process. By familiarizing oneself with these tools and their functions, one can achieve a higher level of proficiency in BGA reballing, ultimately leading to more reliable and effective repairs.
Step-by-Step Guide to Preparing a BGA Chip for Reballing
On the third day of mastering advanced microsoldering techniques, the focus shifts to the intricate process of preparing a Ball Grid Array (BGA) chip for reballing. This step is crucial for ensuring the successful reattachment of the chip to a circuit board, and it requires precision and attention to detail. To begin with, it is essential to understand the importance of a clean and well-prepared BGA chip. Any residual solder or debris can lead to poor connections and potential failure of the chip once it is reattached. Therefore, the first step in the preparation process involves carefully removing the old solder from the chip.
To achieve this, one must employ a soldering iron with a fine tip, which allows for precise control and minimizes the risk of damaging the chip. Gently heating the solder balls on the BGA chip will cause them to melt, at which point a solder wick can be used to absorb the molten solder. It is important to work methodically, ensuring that all solder is removed from each pad on the chip. This process may need to be repeated several times to ensure complete removal of the old solder.
Once the old solder has been removed, the next step involves cleaning the BGA chip to remove any flux residue or other contaminants. A high-quality isopropyl alcohol solution is recommended for this task, as it effectively dissolves and removes residues without leaving any harmful deposits. Using a lint-free cloth or a specialized cleaning swab, gently wipe the surface of the chip, paying particular attention to the pads where the solder balls will be reattached. This cleaning process is vital for ensuring that the new solder balls adhere properly to the chip.
Following the cleaning, it is necessary to inspect the BGA chip for any signs of damage or wear. This inspection should be conducted under a microscope, as even the smallest imperfections can lead to issues during reballing. Look for any scratches, dents, or other irregularities on the chip’s surface, particularly around the pads. If any damage is detected, it may be necessary to repair or replace the chip before proceeding with the reballing process.
With the chip cleaned and inspected, the next step is to apply a thin layer of flux to the pads. Flux is a chemical cleaning agent that helps to improve the flow of solder and ensures a strong bond between the solder balls and the chip. It is important to apply the flux evenly across all pads, as uneven application can lead to inconsistent soldering results. A small brush or a specialized flux pen can be used to apply the flux with precision.
Finally, the BGA chip is ready for the reballing process. This involves placing a stencil over the chip, aligning it carefully with the pads, and then applying solder paste to the stencil. The solder paste contains tiny solder balls that will form the new connections on the chip. Once the paste is applied, the stencil is removed, and the chip is heated to melt the solder balls, forming new, uniform connections.
In conclusion, preparing a BGA chip for reballing is a meticulous process that requires careful attention to detail and precision at every step. By following these guidelines, one can ensure that the chip is properly prepared for reballing, setting the stage for a successful reattachment to the circuit board.
Mastering the Art of Solder Ball Placement for BGA Reballing
On the third day of mastering BGA reballing, the focus shifts to the intricate art of solder ball placement, a critical step that demands precision and skill. As one delves deeper into advanced microsoldering techniques, understanding the nuances of this process becomes paramount. The BGA, or Ball Grid Array, is a type of surface-mount packaging used for integrated circuits, and reballing involves replacing or reapplying the solder balls that connect the chip to the circuit board. This process is essential for repairing or refurbishing electronic devices, ensuring their functionality and longevity.
To begin with, the preparation of the BGA chip is crucial. It involves cleaning the chip meticulously to remove any residual solder or contaminants that might interfere with the new solder balls’ adhesion. This is typically achieved using a combination of heat and specialized cleaning agents, which help in achieving a pristine surface. Once the chip is prepared, the next step involves aligning the stencil, a thin sheet with holes corresponding to the solder ball pattern, over the chip. This alignment is critical, as even the slightest misalignment can lead to connectivity issues, rendering the reballing process ineffective.
With the stencil in place, the application of solder paste follows. The paste, composed of tiny solder particles suspended in flux, is spread evenly across the stencil using a squeegee. This ensures that each hole in the stencil is filled with the right amount of paste, which will later form the solder balls. The uniformity of the paste application is vital, as it directly impacts the size and shape of the solder balls, which in turn affects the electrical connections.
Once the paste is applied, the next phase involves the removal of the stencil, revealing the precisely placed solder paste deposits on the chip. At this juncture, the chip is ready for the reflow process, where it is subjected to controlled heat. This heat causes the solder paste to melt and form spherical balls, which solidify upon cooling. The reflow process requires careful monitoring of temperature profiles to ensure that the solder balls form correctly without causing thermal damage to the chip or the board.
After the reflow, inspection becomes imperative. Advanced techniques such as X-ray imaging or optical inspection are employed to verify the integrity and placement of the solder balls. This step is crucial in identifying any defects such as bridging, where solder balls may have inadvertently connected, or voids, which are gaps within the solder that can compromise electrical performance. Addressing these issues promptly ensures the reliability of the reballing process.
In conclusion, mastering the art of solder ball placement for BGA reballing is a meticulous process that requires a blend of precision, skill, and advanced technology. As one progresses through the stages of preparation, alignment, application, reflow, and inspection, the importance of each step becomes evident. By adhering to these advanced microsoldering techniques, technicians can ensure robust and reliable connections, thereby extending the life and performance of electronic devices. As technology continues to evolve, so too will the methods and tools used in BGA reballing, underscoring the need for continuous learning and adaptation in this specialized field.
Common Mistakes in BGA Reballing and How to Avoid Them
On the third day of mastering BGA reballing, technicians often encounter a series of common mistakes that can impede their progress and affect the quality of their work. Understanding these pitfalls and learning how to avoid them is crucial for anyone aspiring to excel in advanced microsoldering techniques. One of the most frequent errors is the improper removal of the old solder balls. This step is critical, as any residual solder can lead to uneven surfaces, which in turn causes poor contact between the BGA and the PCB. To avoid this, it is essential to use the right tools and techniques, such as a high-quality solder wick and a precise temperature-controlled soldering iron, to ensure a clean and even surface.
Another common mistake is the misalignment of the BGA chip during the reballing process. Misalignment can result in poor electrical connections, leading to device malfunction. To prevent this, technicians should employ alignment tools and templates that help position the BGA accurately over the PCB pads. Additionally, using a microscope can provide the necessary magnification to ensure precise alignment, allowing for a more reliable connection.
Furthermore, insufficient or excessive heat application during the reflow process is a prevalent issue. Applying too little heat can result in incomplete solder melting, while too much heat can damage the BGA or the PCB. To mitigate this risk, it is vital to use a reflow profile that matches the specific requirements of the components being worked on. This involves carefully monitoring the temperature and time settings on the reflow station to ensure that the solder balls melt and solidify correctly, forming strong and reliable joints.
Contamination is another factor that can compromise the success of BGA reballing. Dust, oils, and other contaminants can interfere with the soldering process, leading to weak joints or complete failure. To avoid contamination, technicians should work in a clean environment and use anti-static tools and materials. Additionally, cleaning the BGA and PCB with isopropyl alcohol before starting the reballing process can help remove any residues that might affect the soldering quality.
Moreover, the choice of solder paste is critical in achieving successful reballing. Using the wrong type of solder paste can lead to poor adhesion and weak joints. It is important to select a solder paste that is compatible with the BGA and PCB materials, as well as one that has the appropriate melting point for the reflow process. Consulting the manufacturer’s specifications and guidelines can provide valuable insights into the most suitable solder paste for a given application.
Finally, inadequate inspection and testing after the reballing process can result in undetected issues that may cause device failure later on. It is essential to conduct thorough inspections using tools such as X-ray machines or automated optical inspection systems to verify the integrity of the solder joints. Additionally, functional testing of the device can help ensure that the reballing process was successful and that the BGA is operating as intended.
In conclusion, mastering BGA reballing requires attention to detail and a thorough understanding of the common mistakes that can occur during the process. By employing the right tools, techniques, and materials, and by maintaining a clean working environment, technicians can avoid these pitfalls and achieve high-quality results. As with any advanced skill, practice and experience are key to refining one’s abilities and achieving mastery in microsoldering techniques.
Advanced Techniques for Ensuring Perfect BGA Alignment
On the third day of mastering BGA reballing, the focus shifts to advanced microsoldering techniques that ensure perfect BGA alignment. As one delves deeper into the intricacies of this delicate process, it becomes evident that precision and attention to detail are paramount. The journey begins with understanding the significance of BGA alignment in the broader context of electronic repair and manufacturing. Ball Grid Array (BGA) components are integral to modern electronics, offering a compact and efficient means of connecting integrated circuits to printed circuit boards (PCBs). However, their small size and dense pin configuration present unique challenges, making precise alignment crucial for functionality and reliability.
To achieve perfect BGA alignment, it is essential to first appreciate the role of the stencil in the reballing process. The stencil serves as a guide, ensuring that solder balls are placed accurately on the BGA pads. Selecting the appropriate stencil, one that matches the specific BGA package, is a critical step. Moreover, the stencil must be meticulously cleaned and maintained to prevent any obstructions that could lead to misalignment. As the process unfolds, the application of solder paste through the stencil requires a steady hand and a keen eye. The paste must be evenly distributed to ensure uniformity in the solder balls, which directly impacts the alignment and eventual connectivity of the BGA.
Transitioning from preparation to execution, the reflow process emerges as a pivotal stage in achieving perfect alignment. The reflow oven’s temperature profile must be carefully calibrated to accommodate the specific thermal characteristics of the BGA and the PCB. A gradual ramp-up in temperature, followed by a controlled cooling phase, ensures that the solder balls melt and solidify uniformly, securing the BGA in its intended position. During this phase, the use of a high-quality flux is indispensable. Flux not only facilitates the flow of solder but also prevents oxidation, which can compromise alignment and lead to connectivity issues.
As one progresses, the importance of inspection cannot be overstated. Advanced techniques such as X-ray imaging and optical inspection provide invaluable insights into the alignment and integrity of the reballing process. These tools allow for the detection of misalignments, bridging, or voids that may not be visible to the naked eye. By identifying and addressing these issues early, one can prevent costly rework and ensure the longevity of the electronic device.
Furthermore, the role of environmental factors in BGA alignment should not be overlooked. Humidity, temperature fluctuations, and static electricity can all influence the reballing process. Implementing stringent environmental controls, such as maintaining a cleanroom environment and using anti-static measures, can significantly enhance the precision of BGA alignment.
In conclusion, mastering BGA reballing on day three involves a comprehensive understanding of advanced microsoldering techniques that ensure perfect alignment. From selecting the right stencil and applying solder paste to executing a precise reflow process and conducting thorough inspections, each step is critical to achieving optimal results. By embracing these advanced techniques and maintaining a meticulous approach, one can overcome the challenges of BGA alignment and contribute to the production of reliable and high-performing electronic devices.
Quality Control and Testing After BGA Reballing
On the third day of mastering BGA reballing, the focus shifts to quality control and testing, crucial steps that ensure the integrity and functionality of the reworked components. After the meticulous process of reballing, which involves removing the old solder balls, cleaning the BGA pads, and applying new solder balls, it is imperative to verify that the reballing has been executed flawlessly. This verification process is essential to prevent potential failures in the field, which could lead to costly repairs or replacements.
To begin with, visual inspection is the first line of defense in quality control. Using a high-powered microscope, technicians examine the BGA component to ensure that the solder balls are uniformly placed and properly aligned with the pads. This step is critical because any misalignment or irregularity can lead to poor electrical connections, which may cause intermittent failures or complete device malfunction. Moreover, visual inspection helps identify any solder bridges or voids that could compromise the component’s performance.
Following visual inspection, X-ray analysis is employed to provide a more in-depth examination of the reballing process. This non-destructive testing method allows technicians to see beneath the surface, revealing hidden defects such as voids within the solder balls or incomplete solder joints. X-ray analysis is particularly valuable because it can detect issues that are not visible to the naked eye, thus ensuring a higher level of reliability and performance in the final product.
In addition to X-ray analysis, electrical testing is conducted to verify the functionality of the reballing process. This involves checking the continuity and resistance of the solder joints to ensure that they meet the required specifications. By applying a small current through the BGA component, technicians can measure the electrical characteristics of each solder joint, identifying any anomalies that may indicate a defective connection. This step is crucial because it confirms that the reballing process has restored the component to its original operational state.
Furthermore, thermal cycling tests are often performed to assess the durability of the reballing under varying temperature conditions. This involves subjecting the BGA component to repeated cycles of heating and cooling, simulating the thermal stresses it will encounter during normal operation. By doing so, technicians can evaluate the long-term reliability of the solder joints, ensuring that they can withstand the rigors of real-world applications without failure.
Finally, it is important to document all findings and results from the quality control and testing procedures. Detailed records provide a comprehensive overview of the reballing process, allowing for traceability and accountability. This documentation is invaluable for future reference, particularly if any issues arise with the component after it has been deployed.
In conclusion, quality control and testing are indispensable components of the BGA reballing process. By employing a combination of visual inspection, X-ray analysis, electrical testing, and thermal cycling, technicians can ensure that the reballing has been performed to the highest standards. These rigorous testing procedures not only guarantee the functionality and reliability of the reworked components but also contribute to the overall success and reputation of the microsoldering operation. As such, mastering these techniques on day three is a pivotal step in becoming proficient in advanced microsoldering practices.
Q&A
1. **What is BGA reballing?**
BGA reballing is the process of replacing or restoring the solder balls on a Ball Grid Array (BGA) component to ensure proper electrical connections.
2. **Why is BGA reballing important in microsoldering?**
It is crucial for repairing or refurbishing electronic devices, as it restores functionality to components with faulty or damaged solder joints.
3. **What tools are essential for BGA reballing?**
Essential tools include a hot air rework station, soldering iron, BGA reballing kit (stencils, flux, solder balls), and a microscope for precision work.
4. **What are the key steps in the BGA reballing process?**
Key steps include removing the BGA chip, cleaning the old solder, applying flux, aligning the stencil, placing solder balls, and reflowing the solder.
5. **What challenges might one face during BGA reballing?**
Challenges include maintaining precise temperature control, avoiding damage to the chip or PCB, and ensuring proper alignment of solder balls.
6. **How can one ensure quality in BGA reballing?**
Quality can be ensured by using high-quality materials, maintaining a clean work environment, and performing thorough inspections with a microscope.On Day Three of mastering BGA reballing in advanced microsoldering techniques, participants should have developed a comprehensive understanding of the intricate processes involved in reballing ball grid array components. By this stage, they should be proficient in the use of specialized tools and equipment, such as rework stations and stencils, and be able to execute precise alignment and soldering of BGA components. The focus on hands-on practice and troubleshooting common issues ensures that participants can confidently apply these skills in real-world scenarios, enhancing their ability to repair and maintain complex electronic devices. Overall, Day Three solidifies the foundational knowledge and technical expertise necessary for successful BGA reballing, marking a significant milestone in the journey toward becoming a skilled microsoldering technician.
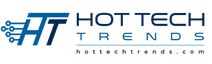