In recent years, the field of robotics has witnessed remarkable advancements, particularly in the realm of robotic dexterity. These breakthroughs are revolutionizing industries by enhancing the precision, adaptability, and efficiency of robotic systems. Our latest innovations in robotic dexterity are pushing the boundaries of what machines can achieve, enabling them to perform complex tasks with a level of finesse and agility that was once thought to be the exclusive domain of human hands. From intricate surgical procedures to delicate assembly lines, these cutting-edge developments are not only transforming the capabilities of robots but also expanding their applications across various sectors. By integrating advanced sensors, machine learning algorithms, and sophisticated control systems, our innovations are setting new standards in robotic performance, paving the way for a future where robots can seamlessly collaborate with humans in dynamic environments.
Advancements In Robotic Grasping Techniques
In recent years, the field of robotics has witnessed remarkable advancements, particularly in the domain of robotic grasping techniques. These innovations have been driven by the need for robots to perform tasks with a level of dexterity and precision that closely mimics human capabilities. As industries increasingly rely on automation, the demand for robots that can handle delicate and complex tasks has surged, prompting researchers and engineers to explore new methodologies and technologies.
One of the most significant breakthroughs in robotic grasping is the development of soft robotics. Unlike traditional rigid robotic arms, soft robots are constructed from flexible materials that allow for a more nuanced interaction with objects. This flexibility enables them to grasp items of varying shapes and sizes without causing damage, a crucial requirement in industries such as agriculture and healthcare. By employing materials like silicone and rubber, soft robots can adapt their grip to the contours of an object, providing a level of versatility that was previously unattainable with conventional robotic systems.
In addition to material innovations, advancements in sensor technology have played a pivotal role in enhancing robotic dexterity. Modern robots are equipped with sophisticated sensors that provide real-time feedback on the force and pressure being applied during a grasp. This sensory input allows robots to adjust their grip dynamically, ensuring that they can handle fragile items with care. Furthermore, the integration of machine learning algorithms enables these robots to learn from past interactions, improving their grasping techniques over time. By analyzing data from previous tasks, robots can refine their approach, leading to more efficient and effective performance.
Another noteworthy development is the use of computer vision in robotic grasping. By employing advanced cameras and image processing algorithms, robots can identify and assess objects in their environment with remarkable accuracy. This capability is particularly beneficial in unstructured settings, where robots must navigate and manipulate a diverse array of items. Computer vision allows robots to recognize objects, determine their orientation, and plan the most appropriate grasping strategy. Consequently, robots can perform tasks that require a high degree of precision, such as assembling intricate components or sorting items in a warehouse.
Moreover, the advent of collaborative robots, or cobots, has further expanded the potential applications of robotic grasping techniques. Designed to work alongside humans, cobots are equipped with safety features that enable them to operate in close proximity to people without posing a risk. This collaboration allows for a seamless integration of human intuition and robotic precision, resulting in enhanced productivity and efficiency. In manufacturing settings, for instance, cobots can take on repetitive or strenuous tasks, freeing human workers to focus on more complex and creative endeavors.
As we continue to push the boundaries of what robots can achieve, the future of robotic grasping techniques looks promising. Ongoing research and development efforts are focused on creating even more sophisticated systems that can handle an ever-expanding range of tasks. From delicate surgical procedures to intricate assembly lines, the potential applications are vast and varied. As these technologies mature, we can expect to see robots playing an increasingly integral role in our daily lives, transforming industries and improving the quality of life for people around the world. Through continued innovation and collaboration, the quest for robotic dexterity will undoubtedly yield exciting and transformative results.
Precision Control In Robotic Surgery
In recent years, the field of robotic surgery has witnessed remarkable advancements, particularly in the realm of precision control. These breakthroughs in robotic dexterity have not only enhanced the capabilities of surgical robots but have also significantly improved patient outcomes. As we delve into the intricacies of these innovations, it becomes evident that the integration of cutting-edge technology with surgical expertise is reshaping the landscape of modern medicine.
To begin with, the development of more sophisticated robotic systems has been pivotal in achieving greater precision during surgical procedures. These systems are equipped with advanced sensors and actuators that allow for meticulous control over surgical instruments. By mimicking the dexterity of the human hand, these robots can perform complex tasks with unparalleled accuracy. This level of precision is particularly crucial in delicate surgeries, such as those involving the brain or heart, where even the slightest error can have dire consequences.
Moreover, the incorporation of artificial intelligence (AI) into robotic surgery has further enhanced precision control. AI algorithms can analyze vast amounts of data in real-time, providing surgeons with valuable insights and recommendations during procedures. This not only aids in decision-making but also allows for the anticipation of potential complications, thereby reducing the risk of errors. Additionally, machine learning techniques enable these systems to continuously improve their performance by learning from past surgeries, thus refining their precision over time.
Another significant innovation in robotic dexterity is the development of haptic feedback technology. This technology provides surgeons with tactile sensations, allowing them to “feel” the tissues they are operating on, despite being physically separated from the patient. Haptic feedback bridges the gap between human touch and robotic precision, offering a level of control that was previously unattainable. This advancement is particularly beneficial in minimally invasive surgeries, where the ability to discern tissue texture and resistance is crucial for successful outcomes.
Furthermore, the miniaturization of robotic components has played a vital role in enhancing precision control. Smaller, more agile robotic arms can navigate through the human body with greater ease, reaching areas that were once considered inaccessible. This has expanded the scope of robotic surgery, enabling procedures that were previously deemed too risky or complex. The ability to operate with such precision not only minimizes trauma to surrounding tissues but also accelerates patient recovery times.
In addition to these technological advancements, the collaboration between engineers and medical professionals has been instrumental in driving innovation in robotic surgery. By working closely together, these experts can tailor robotic systems to meet the specific needs of various surgical disciplines. This interdisciplinary approach ensures that the technology is not only cutting-edge but also practical and effective in real-world applications.
As we look to the future, the potential for further breakthroughs in robotic dexterity is immense. Ongoing research and development efforts are focused on enhancing the adaptability and autonomy of surgical robots, paving the way for even more precise and efficient procedures. With each new innovation, the boundaries of what is possible in robotic surgery continue to expand, promising a future where precision control is not just an aspiration but a standard of care.
In conclusion, the latest innovations in robotic dexterity have revolutionized precision control in robotic surgery. Through the integration of advanced technology, AI, haptic feedback, and miniaturization, these systems have achieved unprecedented levels of accuracy and control. As collaboration between engineers and medical professionals continues to drive progress, the future of robotic surgery holds the promise of even greater advancements, ultimately transforming the way we approach surgical care.
Enhanced Tactile Feedback Systems
In recent years, the field of robotics has witnessed remarkable advancements, particularly in the realm of robotic dexterity. One of the most significant breakthroughs contributing to this progress is the development of enhanced tactile feedback systems. These systems are revolutionizing the way robots interact with their environment, enabling them to perform tasks with a level of precision and sensitivity that was previously unattainable. As we delve into the intricacies of these innovations, it becomes evident that the integration of tactile feedback is a pivotal factor in advancing robotic capabilities.
To begin with, tactile feedback systems are designed to mimic the human sense of touch, allowing robots to perceive and respond to various stimuli. This is achieved through the incorporation of sensors that detect pressure, texture, and temperature, among other factors. By processing this sensory information, robots can adjust their grip and movements in real-time, thereby enhancing their ability to manipulate objects with greater finesse. This development is particularly crucial in applications where delicate handling is required, such as in the assembly of intricate electronic components or in medical procedures where precision is paramount.
Moreover, the implementation of tactile feedback systems in robotics is not limited to industrial applications. In the realm of healthcare, for instance, these systems are being utilized to improve the efficacy of prosthetic limbs. By providing users with a sense of touch, prosthetics equipped with tactile feedback can significantly enhance the quality of life for individuals with limb loss. This innovation allows users to perform everyday tasks with greater ease and confidence, bridging the gap between human and machine interaction.
Transitioning to another aspect, the integration of tactile feedback systems also plays a crucial role in the development of autonomous robots. As these machines are increasingly deployed in unstructured environments, the ability to adapt to varying conditions becomes essential. Tactile feedback enables robots to navigate complex terrains and interact with objects in a manner that is both safe and efficient. For example, in search and rescue operations, robots equipped with these systems can delicately maneuver through debris to locate and assist survivors, demonstrating the potential life-saving applications of this technology.
Furthermore, the advancements in tactile feedback systems are closely linked to the development of artificial intelligence and machine learning algorithms. These technologies work in tandem to process the vast amounts of data generated by the sensors, allowing robots to learn from their interactions and improve their performance over time. This synergy between tactile feedback and AI is paving the way for the creation of robots that can perform tasks with a level of autonomy and adaptability that was once thought to be the realm of science fiction.
In conclusion, the breakthroughs in robotic dexterity, particularly through enhanced tactile feedback systems, are transforming the landscape of robotics. By endowing robots with a sense of touch, these innovations are enabling machines to perform tasks with unprecedented precision and adaptability. As research and development in this field continue to progress, the potential applications of tactile feedback systems are vast and varied, promising to reshape industries and improve lives in ways we are only beginning to imagine. The future of robotics, bolstered by these advancements, holds immense promise, heralding a new era of interaction between humans and machines.
Machine Learning For Dexterous Manipulation
In recent years, the field of robotics has witnessed remarkable advancements, particularly in the realm of dexterous manipulation. This progress is largely attributed to the integration of machine learning techniques, which have significantly enhanced the ability of robots to perform complex tasks with precision and adaptability. As we delve into the intricacies of machine learning for dexterous manipulation, it becomes evident that these innovations are paving the way for a new era of robotic capabilities.
To begin with, the concept of dexterous manipulation involves the ability of robots to handle objects with a level of finesse and control akin to human hands. This requires not only precise motor skills but also the capacity to adapt to varying conditions and object properties. Machine learning, with its ability to process vast amounts of data and learn from it, has emerged as a crucial tool in achieving these objectives. By employing algorithms that enable robots to learn from experience, researchers have developed systems that can improve their performance over time, thereby enhancing their dexterity.
One of the key breakthroughs in this domain is the use of reinforcement learning, a subset of machine learning that focuses on training models through trial and error. In the context of robotic manipulation, reinforcement learning allows robots to explore different strategies for handling objects and receive feedback on their performance. This iterative process enables the robot to refine its techniques, ultimately leading to more efficient and effective manipulation. For instance, robots can now learn to adjust their grip based on the weight and texture of an object, ensuring a secure hold without causing damage.
Moreover, the integration of deep learning has further propelled advancements in robotic dexterity. Deep learning models, particularly convolutional neural networks, have been instrumental in enabling robots to perceive and interpret their environment with greater accuracy. By processing visual data, these models allow robots to identify objects, assess their orientation, and determine the optimal approach for manipulation. This capability is crucial for tasks that require a high degree of precision, such as assembling intricate components or handling delicate materials.
In addition to these techniques, the development of simulation environments has played a pivotal role in advancing machine learning for dexterous manipulation. Simulations provide a safe and controlled setting for robots to practice and hone their skills without the risk of damage or injury. By simulating various scenarios and object interactions, researchers can gather valuable data that informs the training of machine learning models. This approach not only accelerates the learning process but also enhances the robot’s ability to generalize its skills to real-world applications.
Furthermore, the collaboration between academia and industry has been instrumental in driving these innovations. By pooling resources and expertise, researchers and engineers have been able to tackle complex challenges and develop solutions that push the boundaries of what robots can achieve. This synergy has led to the creation of robotic systems that are not only more dexterous but also more versatile, capable of performing a wide range of tasks across different sectors.
In conclusion, the integration of machine learning into robotic systems has ushered in a new era of dexterous manipulation. Through techniques such as reinforcement learning and deep learning, robots are now able to perform tasks with unprecedented precision and adaptability. As research continues to advance, we can expect even greater breakthroughs that will further enhance the capabilities of robotic systems, ultimately transforming industries and improving our daily lives.
Soft Robotics And Adaptive Gripping
In recent years, the field of robotics has witnessed remarkable advancements, particularly in the realm of soft robotics and adaptive gripping. These innovations have significantly enhanced robotic dexterity, enabling machines to perform tasks with a level of finesse and adaptability previously thought to be exclusive to human hands. The development of soft robotics, which involves the use of flexible materials and structures, has been pivotal in this transformation. Unlike traditional rigid robots, soft robots can manipulate objects with varying shapes and fragility, making them ideal for applications in diverse industries such as healthcare, agriculture, and manufacturing.
One of the key breakthroughs in soft robotics is the creation of adaptive grippers that mimic the human hand’s ability to grasp and manipulate objects. These grippers are designed with materials that can change their shape and stiffness in response to external stimuli, allowing them to handle a wide range of items with precision. For instance, in the food industry, adaptive grippers can delicately pick and place fruits and vegetables without causing damage, thereby improving efficiency and reducing waste. This capability is achieved through the integration of advanced sensors and actuators that provide real-time feedback, enabling the robot to adjust its grip dynamically.
Moreover, the incorporation of artificial intelligence and machine learning algorithms has further enhanced the functionality of soft robotic systems. By analyzing data from sensors, these algorithms enable robots to learn from their interactions with objects, improving their performance over time. This learning capability is crucial for tasks that require a high degree of dexterity, such as assembling intricate components in electronics manufacturing or performing delicate surgical procedures. As a result, robots equipped with adaptive gripping technology are becoming indispensable tools in environments where precision and adaptability are paramount.
In addition to their practical applications, these innovations in robotic dexterity are also driving research in biomimicry, where engineers draw inspiration from nature to design more efficient and versatile robotic systems. For example, the study of octopus tentacles and elephant trunks has led to the development of grippers that can wrap around objects, providing a secure hold without exerting excessive force. This approach not only enhances the robot’s ability to handle irregularly shaped items but also opens up new possibilities for exploration in environments that are challenging for traditional robots, such as underwater or space missions.
Furthermore, the advancements in soft robotics and adaptive gripping are fostering collaboration between various disciplines, including materials science, computer science, and mechanical engineering. This interdisciplinary approach is essential for overcoming the technical challenges associated with creating robots that can operate safely and effectively alongside humans. As these technologies continue to evolve, they hold the promise of transforming industries by automating complex tasks, improving productivity, and reducing the risk of injury in hazardous environments.
In conclusion, the breakthroughs in robotic dexterity, particularly in the areas of soft robotics and adaptive gripping, represent a significant leap forward in the capabilities of robotic systems. By combining flexible materials, advanced sensors, and intelligent algorithms, these innovations are enabling robots to perform tasks with unprecedented precision and adaptability. As research and development in this field progress, we can expect to see even more sophisticated robotic solutions that will redefine the boundaries of what machines can achieve, ultimately enhancing our ability to tackle complex challenges across various sectors.
Real-Time Motion Planning In Robotics
In recent years, the field of robotics has witnessed remarkable advancements, particularly in the realm of robotic dexterity. These breakthroughs have been largely driven by innovations in real-time motion planning, a critical component that enables robots to perform complex tasks with precision and adaptability. As we delve into the intricacies of these developments, it becomes evident that the integration of sophisticated algorithms and cutting-edge technology is revolutionizing the capabilities of robotic systems.
To begin with, real-time motion planning is essential for robots to navigate dynamic environments and execute tasks that require a high degree of precision. Traditionally, robots operated in controlled settings where their movements were pre-programmed and predictable. However, the demand for robots that can function autonomously in unpredictable environments has necessitated the development of more advanced motion planning techniques. These techniques allow robots to assess their surroundings, make decisions, and adjust their actions in real-time, thereby enhancing their ability to perform tasks with human-like dexterity.
One of the key innovations in this area is the use of machine learning algorithms to improve motion planning. By leveraging large datasets and powerful computational models, robots can learn from past experiences and refine their movements over time. This approach not only enhances the accuracy of their actions but also enables them to adapt to new and unforeseen challenges. For instance, a robot equipped with machine learning capabilities can adjust its grip on an object based on its shape and texture, ensuring a secure hold without causing damage.
Moreover, the integration of sensor technology has played a pivotal role in advancing robotic dexterity. Sensors provide robots with real-time feedback about their environment, allowing them to make informed decisions about their movements. For example, tactile sensors can mimic the sense of touch, enabling robots to gauge the pressure needed to handle delicate objects. Similarly, vision sensors allow robots to perceive their surroundings and identify obstacles, facilitating smoother navigation and task execution.
In addition to these technological advancements, the development of more sophisticated control systems has further enhanced robotic dexterity. These systems enable robots to coordinate multiple joints and actuators simultaneously, resulting in fluid and natural movements. By employing advanced control algorithms, robots can achieve a level of precision and agility that was previously unattainable. This is particularly beneficial in applications such as surgical robotics, where even the slightest error can have significant consequences.
Furthermore, the collaboration between academia and industry has been instrumental in driving these innovations. Research institutions and companies are working together to develop new algorithms, test prototypes, and refine existing technologies. This synergy has accelerated the pace of innovation, leading to the rapid deployment of advanced robotic systems across various sectors, including manufacturing, healthcare, and logistics.
As we look to the future, it is clear that the continued evolution of real-time motion planning will unlock new possibilities for robotic applications. The ability of robots to perform complex tasks with dexterity and precision will not only enhance productivity but also improve safety and efficiency in numerous industries. While challenges remain, particularly in terms of computational power and energy efficiency, the progress made thus far is a testament to the potential of robotics to transform the way we live and work.
In conclusion, the breakthroughs in robotic dexterity, driven by advancements in real-time motion planning, represent a significant leap forward in the field of robotics. Through the integration of machine learning, sensor technology, and sophisticated control systems, robots are becoming increasingly capable of performing tasks with a level of precision and adaptability that rivals human abilities. As research and development continue to push the boundaries of what is possible, the future of robotics holds immense promise for innovation and progress.
Q&A
1. **What is robotic dexterity?**
Robotic dexterity refers to the ability of robots to manipulate objects with precision and skill, similar to human hand movements.
2. **What are some recent breakthroughs in robotic dexterity?**
Recent breakthroughs include advancements in machine learning algorithms that enable robots to learn complex tasks, the development of soft robotics for more adaptable grip, and improved sensor technologies for better object recognition and manipulation.
3. **How do machine learning algorithms enhance robotic dexterity?**
Machine learning algorithms allow robots to learn from experience, improving their ability to perform tasks by adapting to new situations and refining their movements over time.
4. **What role do soft robotics play in improving dexterity?**
Soft robotics use flexible materials that mimic the adaptability of human muscles, allowing robots to handle delicate objects without causing damage and to adjust their grip dynamically.
5. **How have sensor technologies contributed to robotic dexterity?**
Advanced sensor technologies provide robots with detailed feedback about their environment, enabling precise control over their movements and improving their ability to interact with various objects.
6. **What are the potential applications of improved robotic dexterity?**
Improved robotic dexterity can be applied in fields such as manufacturing, healthcare, and service industries, where robots can perform complex tasks like assembling intricate components, assisting in surgeries, or handling fragile items.Breakthroughs in robotic dexterity have significantly advanced the capabilities of robots, enabling them to perform complex tasks with precision and adaptability. Recent innovations have focused on enhancing the fine motor skills of robotic systems, allowing them to manipulate objects with a level of finesse previously unattainable. These advancements are driven by improvements in sensor technology, machine learning algorithms, and the integration of soft robotics, which together enable robots to better understand and interact with their environments. The development of more sophisticated grippers and tactile sensors has also played a crucial role, providing robots with the ability to handle delicate and irregularly shaped objects. As a result, these innovations are expanding the potential applications of robots across various industries, from manufacturing and healthcare to service and domestic environments. The continued evolution of robotic dexterity promises to revolutionize the way robots are utilized, making them more versatile and efficient partners in both professional and everyday settings.
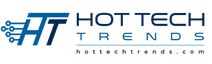