Breakthroughs in robotic dexterity have marked a significant leap forward in the field of robotics, transforming the way machines interact with their environment and perform complex tasks. Recent innovations have focused on enhancing the precision, adaptability, and sensory capabilities of robotic systems, enabling them to execute intricate maneuvers with a level of finesse previously reserved for human hands. These advancements are driven by cutting-edge developments in artificial intelligence, machine learning, and sensor technology, which collectively empower robots to learn from their surroundings, make real-time decisions, and adapt to dynamic conditions. As a result, robotic dexterity is now being harnessed across various industries, from manufacturing and healthcare to logistics and beyond, promising to revolutionize productivity and efficiency while opening new frontiers for automation.
Enhancing Precision: The Role of AI in Robotic Dexterity
In recent years, the field of robotics has witnessed remarkable advancements, particularly in the realm of robotic dexterity. This progress is largely attributed to the integration of artificial intelligence (AI), which has significantly enhanced the precision and adaptability of robotic systems. As we delve into the intricacies of these innovations, it becomes evident that AI plays a pivotal role in transforming robotic dexterity from a theoretical concept into a practical reality.
To begin with, the incorporation of AI into robotic systems has enabled machines to perform tasks with a level of precision that was previously unattainable. Traditional robotic systems relied heavily on pre-programmed instructions, which limited their ability to adapt to dynamic environments. However, with the advent of AI, robots can now learn from their surroundings and make real-time adjustments. This capability is particularly crucial in industries such as manufacturing and healthcare, where precision is paramount. For instance, in surgical robotics, AI-driven systems can analyze vast amounts of data to assist surgeons in performing intricate procedures with unparalleled accuracy.
Moreover, AI enhances robotic dexterity by enabling machines to understand and interpret complex sensory inputs. Through machine learning algorithms, robots can process visual, auditory, and tactile information, allowing them to interact with their environment in a more human-like manner. This sensory integration is essential for tasks that require fine motor skills, such as assembling delicate components or handling fragile objects. By mimicking human sensory perception, AI-powered robots can execute these tasks with a level of finesse that was once thought to be exclusive to human operators.
In addition to improving precision, AI also facilitates the development of more versatile robotic systems. Traditional robots were often designed for specific tasks, limiting their applicability across different domains. However, AI enables robots to learn and adapt to new tasks without the need for extensive reprogramming. This adaptability is achieved through techniques such as reinforcement learning, where robots learn optimal behaviors through trial and error. As a result, AI-driven robots can seamlessly transition between tasks, making them invaluable assets in environments that demand flexibility and efficiency.
Furthermore, the role of AI in enhancing robotic dexterity extends beyond individual machines to encompass entire robotic networks. Through cloud-based AI platforms, robots can share data and learn from each other’s experiences, leading to collective intelligence. This interconnectedness allows for the rapid dissemination of knowledge and skills across robotic systems, accelerating the pace of innovation. For example, in logistics and warehousing, AI-powered robots can collaborate to optimize inventory management and streamline supply chain operations, thereby improving overall productivity.
Despite these advancements, challenges remain in the quest to perfect robotic dexterity. Ensuring the safety and reliability of AI-driven systems is of paramount importance, particularly in applications where human lives are at stake. Researchers are actively working on developing robust algorithms that can guarantee the safe operation of robots in unpredictable environments. Additionally, ethical considerations surrounding the use of AI in robotics must be addressed to ensure that these technologies are deployed responsibly and equitably.
In conclusion, the integration of AI into robotic systems has revolutionized the field of robotic dexterity, enabling machines to perform tasks with unprecedented precision and adaptability. As AI continues to evolve, we can expect further breakthroughs that will expand the capabilities of robots and redefine their role in society. By harnessing the power of AI, we are not only enhancing the precision of robotic systems but also paving the way for a future where humans and robots work together in harmony to achieve common goals.
Soft Robotics: Mimicking Human Touch for Delicate Tasks
In recent years, the field of robotics has witnessed remarkable advancements, particularly in the realm of soft robotics, which aims to mimic the nuanced dexterity of human touch. This burgeoning area of research focuses on creating robots capable of performing delicate tasks with precision and care, a feat that has long eluded traditional rigid robotic systems. The latest innovations in soft robotics are poised to revolutionize industries ranging from healthcare to manufacturing, offering solutions that were once thought to be the exclusive domain of human hands.
One of the primary challenges in developing soft robotic systems is replicating the intricate sensory feedback and adaptability of human touch. Unlike their rigid counterparts, soft robots are constructed from flexible materials that allow for a greater range of motion and adaptability. These materials, often inspired by biological tissues, enable robots to interact with their environment in a more nuanced manner. For instance, the integration of advanced sensors within these materials allows soft robots to detect subtle changes in pressure and texture, thereby facilitating tasks that require a gentle touch, such as handling fragile objects or performing intricate surgical procedures.
Moreover, the development of soft actuators has been instrumental in enhancing the dexterity of robotic systems. These actuators, which function as the muscles of soft robots, are designed to mimic the natural movements of human muscles. By utilizing materials such as elastomers and hydrogels, researchers have created actuators that can contract and expand in response to external stimuli, allowing for smooth and precise movements. This capability is particularly beneficial in applications where precision is paramount, such as in the assembly of delicate electronic components or the harvesting of soft fruits.
In addition to material innovations, advancements in artificial intelligence and machine learning have played a crucial role in the evolution of soft robotics. By leveraging these technologies, researchers have developed algorithms that enable robots to learn from their interactions with the environment, thereby improving their performance over time. This learning capability is essential for tasks that require adaptability and problem-solving skills, as it allows robots to adjust their actions based on feedback from their surroundings. Consequently, soft robots are becoming increasingly adept at performing complex tasks that were previously beyond their reach.
Furthermore, the integration of soft robotics into various industries has the potential to enhance efficiency and safety. In the healthcare sector, for example, soft robots can assist surgeons in performing minimally invasive procedures with greater precision, reducing the risk of complications and improving patient outcomes. Similarly, in the manufacturing industry, these robots can handle delicate materials with care, minimizing waste and increasing productivity. As these technologies continue to evolve, the potential applications for soft robotics are virtually limitless.
In conclusion, the latest innovations in soft robotics represent a significant leap forward in our quest to replicate the dexterity of human touch. By combining advances in materials science, artificial intelligence, and machine learning, researchers have developed robotic systems that are capable of performing delicate tasks with unprecedented precision and care. As these technologies continue to mature, they hold the promise of transforming a wide range of industries, offering solutions that enhance both efficiency and safety. The future of soft robotics is indeed bright, and its impact on our world is only just beginning to unfold.
Advanced Sensors: Revolutionizing Robotic Hand-Eye Coordination
In recent years, the field of robotics has witnessed remarkable advancements, particularly in the realm of robotic dexterity. Central to these developments is the integration of advanced sensors, which have significantly enhanced robotic hand-eye coordination. This evolution is not merely a technical upgrade but a transformative leap that is reshaping the capabilities of robots across various industries. As we delve into the intricacies of these innovations, it becomes evident that the synergy between sensors and robotic systems is pivotal in achieving unprecedented levels of precision and adaptability.
To begin with, the role of sensors in robotic systems cannot be overstated. These devices serve as the primary interface between the robot and its environment, providing critical data that informs decision-making processes. In the context of hand-eye coordination, sensors enable robots to perceive their surroundings with remarkable accuracy. This perception is akin to the human ability to visually assess and manipulate objects, a skill that has long been a challenge for robotic systems. By employing a combination of visual, tactile, and proprioceptive sensors, robots can now perform tasks that require a high degree of dexterity, such as assembling intricate components or handling delicate materials.
Moreover, the integration of machine learning algorithms with sensor data has further propelled advancements in robotic dexterity. These algorithms allow robots to learn from their interactions with the environment, continuously improving their performance over time. For instance, when a robot equipped with advanced sensors attempts to grasp an object, it can analyze feedback from its sensors to adjust its grip in real-time. This adaptive capability is crucial for tasks that involve unpredictable variables, such as varying object shapes or textures. Consequently, robots are becoming more adept at performing complex tasks in dynamic environments, a feat that was previously unattainable.
In addition to enhancing precision, advanced sensors also contribute to the safety and reliability of robotic systems. By providing real-time feedback, sensors enable robots to detect and respond to potential hazards, thereby minimizing the risk of accidents. This is particularly important in collaborative settings where robots and humans work side by side. The ability to swiftly adapt to changes in the environment ensures that robots can operate safely without compromising efficiency. As a result, industries such as manufacturing, healthcare, and logistics are increasingly adopting robotic systems to augment human capabilities and improve operational outcomes.
Furthermore, the miniaturization of sensor technology has opened new avenues for innovation in robotic design. Smaller, more efficient sensors allow for the development of compact robotic systems that can navigate confined spaces with ease. This is particularly beneficial in applications such as search and rescue operations, where robots must maneuver through debris to locate survivors. The combination of advanced sensors and agile robotic platforms is revolutionizing the way we approach challenges in various sectors, offering solutions that were once thought to be beyond reach.
In conclusion, the integration of advanced sensors into robotic systems marks a significant milestone in the quest for enhanced robotic dexterity. By improving hand-eye coordination, these sensors are enabling robots to perform tasks with a level of precision and adaptability that rivals human capabilities. As technology continues to evolve, we can anticipate even greater breakthroughs in robotic dexterity, driven by the relentless pursuit of innovation in sensor technology. This progress not only underscores the potential of robotics to transform industries but also highlights the importance of continued research and development in this dynamic field.
Machine Learning: Teaching Robots to Adapt and Improve
In recent years, the field of robotics has witnessed remarkable advancements, particularly in the realm of robotic dexterity. These breakthroughs are largely attributed to the integration of machine learning techniques, which have significantly enhanced the ability of robots to adapt and improve their performance in dynamic environments. As we delve into the intricacies of these innovations, it becomes evident that machine learning is not merely a tool but a transformative force driving the evolution of robotic capabilities.
At the core of these advancements is the concept of reinforcement learning, a subset of machine learning that enables robots to learn from their interactions with the environment. By employing trial-and-error methods, robots can develop a repertoire of skills that allow them to perform complex tasks with precision. This approach mimics the way humans learn, as it involves receiving feedback from actions and using this information to refine future behavior. Consequently, robots are no longer limited to pre-programmed instructions but can adapt to new situations, making them more versatile and efficient.
Moreover, the integration of deep learning algorithms has further propelled the development of robotic dexterity. These algorithms enable robots to process vast amounts of data and recognize patterns, which is crucial for tasks that require fine motor skills and intricate manipulations. For instance, in manufacturing settings, robots equipped with deep learning capabilities can identify and handle objects of varying shapes and sizes with remarkable accuracy. This level of adaptability is essential for industries that demand high precision and flexibility, as it reduces the need for human intervention and increases overall productivity.
In addition to reinforcement and deep learning, the advent of transfer learning has also played a pivotal role in enhancing robotic dexterity. Transfer learning allows robots to apply knowledge gained from one task to another, thereby accelerating the learning process. This capability is particularly beneficial in scenarios where robots are required to perform a wide range of tasks without extensive retraining. By leveraging previously acquired skills, robots can quickly adapt to new challenges, making them more efficient and cost-effective.
Furthermore, the development of tactile sensors has significantly contributed to the improvement of robotic dexterity. These sensors provide robots with a sense of touch, enabling them to perceive and respond to physical stimuli. When combined with machine learning algorithms, tactile sensors allow robots to perform delicate operations, such as assembling intricate components or handling fragile objects, with a level of finesse that was previously unattainable. This advancement not only enhances the functionality of robots but also expands their potential applications across various sectors, including healthcare, where precision and sensitivity are paramount.
As we continue to explore the potential of machine learning in robotics, it is clear that these innovations are reshaping the landscape of automation. The ability of robots to learn, adapt, and improve autonomously is revolutionizing industries and paving the way for a future where human-robot collaboration is seamless and efficient. While challenges remain, particularly in terms of ensuring safety and ethical considerations, the progress made thus far is a testament to the transformative power of machine learning in enhancing robotic dexterity.
In conclusion, the integration of machine learning techniques has ushered in a new era of robotic dexterity, characterized by adaptability, precision, and efficiency. As research and development in this field continue to advance, we can anticipate even more groundbreaking innovations that will further expand the capabilities of robots, ultimately transforming the way we live and work.
Collaborative Robots: Enhancing Dexterity in Human-Robot Teams
In recent years, the field of robotics has witnessed remarkable advancements, particularly in the realm of collaborative robots, often referred to as cobots. These innovations have significantly enhanced the dexterity of robots, enabling them to work alongside humans more effectively and safely. As industries increasingly integrate these sophisticated machines into their operations, understanding the latest breakthroughs in robotic dexterity becomes crucial.
One of the most significant developments in this area is the improvement of robotic hands and grippers. Traditionally, robots were equipped with simple, rigid grippers that lacked the finesse required for delicate tasks. However, recent innovations have led to the creation of more flexible and sensitive robotic hands. These new designs incorporate advanced materials and sensors that mimic the human hand’s ability to manipulate objects with precision. For instance, soft robotics technology has introduced grippers made from pliable materials that can conform to the shape of an object, allowing for a more secure and gentle grasp. This advancement is particularly beneficial in industries such as electronics and pharmaceuticals, where handling delicate components is essential.
Moreover, the integration of artificial intelligence and machine learning algorithms has further enhanced the dexterity of collaborative robots. By leveraging these technologies, robots can now learn from their interactions and improve their performance over time. This capability is especially valuable in dynamic environments where tasks may vary or require adaptation. For example, in a manufacturing setting, a robot equipped with machine learning can adjust its grip strength and approach based on the specific characteristics of the items it handles. This adaptability not only increases efficiency but also reduces the likelihood of errors or damage.
In addition to improved hardware and software, the development of advanced sensors has played a pivotal role in enhancing robotic dexterity. Modern cobots are equipped with a variety of sensors that provide real-time feedback on their surroundings. These sensors enable robots to detect and respond to changes in their environment, such as the presence of a human coworker or an unexpected obstacle. By processing this information, robots can make split-second decisions to avoid collisions and ensure safe collaboration with human team members. This capability is crucial in settings where humans and robots work in close proximity, such as assembly lines or warehouses.
Furthermore, the concept of human-robot collaboration has been revolutionized by the introduction of intuitive programming interfaces. Traditionally, programming a robot required specialized knowledge and significant time investment. However, recent innovations have led to the development of user-friendly interfaces that allow even non-experts to program robots with ease. These interfaces often utilize visual programming languages or teach-by-demonstration methods, where a human can guide the robot through a task, and the robot subsequently replicates the actions. This approach not only simplifies the programming process but also empowers human workers to customize robotic actions to suit specific needs.
As we continue to explore the potential of collaborative robots, it is evident that these advancements in dexterity are transforming the way humans and robots interact. By enhancing the ability of robots to perform complex tasks with precision and adaptability, industries can achieve greater productivity and safety. As technology progresses, the synergy between human creativity and robotic efficiency promises to unlock new possibilities, paving the way for a future where collaborative robots are integral partners in a wide array of sectors.
Real-World Applications: Robotic Dexterity in Healthcare and Manufacturing
In recent years, the field of robotics has witnessed remarkable advancements, particularly in the realm of robotic dexterity. These innovations have paved the way for significant improvements in both healthcare and manufacturing, two sectors that stand to benefit immensely from enhanced robotic capabilities. As we delve into the real-world applications of robotic dexterity, it becomes evident that these technological breakthroughs are not only transforming industries but also redefining the boundaries of what robots can achieve.
In the healthcare sector, robotic dexterity has emerged as a game-changer, offering unprecedented precision and control in surgical procedures. Surgeons are now able to perform minimally invasive surgeries with the assistance of robotic systems that mimic the intricate movements of the human hand. These systems, equipped with advanced sensors and actuators, allow for greater accuracy and reduced recovery times for patients. For instance, robotic-assisted surgeries in orthopedics and cardiology have demonstrated improved outcomes, as the robots can execute complex tasks with a level of precision that surpasses human capabilities. Moreover, the integration of artificial intelligence with robotic systems has further enhanced their ability to adapt to dynamic surgical environments, thereby increasing the safety and efficacy of medical procedures.
Transitioning to the manufacturing sector, robotic dexterity has revolutionized production lines by enabling robots to perform tasks that require a high degree of precision and adaptability. In industries such as electronics and automotive manufacturing, robots equipped with dexterous capabilities are now able to handle delicate components and assemble intricate parts with remarkable efficiency. This has led to increased productivity and reduced error rates, as robots can consistently perform repetitive tasks without fatigue. Furthermore, the ability of robots to learn and adapt to new tasks through machine learning algorithms has expanded their utility in manufacturing, allowing for greater flexibility in production processes. As a result, companies are able to respond more swiftly to market demands and customize products to meet specific consumer needs.
The convergence of robotic dexterity with other emerging technologies, such as the Internet of Things (IoT) and big data analytics, has further amplified its impact across these sectors. In healthcare, for example, IoT-enabled robotic systems can collect and analyze patient data in real-time, providing valuable insights that inform clinical decisions and improve patient outcomes. Similarly, in manufacturing, data-driven insights can optimize production processes, reduce downtime, and enhance quality control measures. This synergy between robotic dexterity and data analytics is fostering a new era of intelligent automation, where robots are not only tools but also active participants in decision-making processes.
Despite these advancements, challenges remain in the widespread adoption of robotic dexterity. Issues such as high costs, technical complexities, and the need for skilled personnel to operate and maintain these systems pose significant barriers. However, ongoing research and development efforts are focused on addressing these challenges, with the aim of making robotic dexterity more accessible and affordable for a broader range of applications.
In conclusion, the breakthroughs in robotic dexterity are ushering in a new era of innovation in healthcare and manufacturing. By enhancing precision, efficiency, and adaptability, these advancements are transforming the way we approach complex tasks and processes. As technology continues to evolve, the potential for robotic dexterity to drive further progress in these sectors is immense, promising a future where robots play an integral role in improving human lives and advancing industrial capabilities.
Q&A
1. **What is robotic dexterity?**
Robotic dexterity refers to the ability of robots to perform complex manipulation tasks with precision and adaptability, similar to human hand movements.
2. **What are some recent breakthroughs in robotic dexterity?**
Recent breakthroughs include advancements in machine learning algorithms for better grasping techniques, the development of soft robotics for more adaptable manipulation, and improved sensor technologies for enhanced tactile feedback.
3. **How has machine learning contributed to robotic dexterity?**
Machine learning has enabled robots to learn from vast datasets, improving their ability to predict and adapt to various manipulation tasks, leading to more efficient and accurate performance.
4. **What role do sensors play in enhancing robotic dexterity?**
Sensors provide critical feedback on force, pressure, and position, allowing robots to adjust their grip and movements in real-time, which is essential for handling delicate or irregular objects.
5. **What are soft robotics, and how do they improve dexterity?**
Soft robotics involve the use of flexible materials that mimic biological tissues, allowing robots to perform more natural and adaptable movements, which enhances their ability to manipulate a wide range of objects.
6. **What industries benefit from advancements in robotic dexterity?**
Industries such as manufacturing, healthcare, logistics, and agriculture benefit from these advancements, as they enable automation of complex tasks, improve efficiency, and reduce the need for human intervention in hazardous environments.Recent breakthroughs in robotic dexterity have significantly advanced the field, enabling robots to perform complex tasks with greater precision and adaptability. Innovations such as improved sensor technologies, advanced machine learning algorithms, and enhanced mechanical designs have contributed to these advancements. These developments allow robots to manipulate objects with human-like finesse, opening new possibilities in industries like manufacturing, healthcare, and logistics. The integration of tactile feedback and real-time decision-making capabilities further enhances their functionality, making them more versatile and efficient. As these technologies continue to evolve, they promise to revolutionize various sectors by increasing productivity, reducing human error, and expanding the scope of automation.
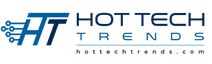